 |
9:00 – 9:30 |
Registration |
9:30 - 10:00 |
- (Broadcasting) Opening Speech
New style of designing based on use of cloud service
- Yasuhiko Fujikawa, President & CEO, VINAS Co., Ltd.
|
|
10:00 - 10:15 |
- Introduction of VINAS weight reduction consulting service.
- Toru Sugino, Director, Marketing Department, VINAS Co., Ltd.
- Weight reduction consulting service of VINAS using non-parametric structural optimization system TOSCA which has been provided for automotive industry and their parts suppliers, heavy industry and other industries will be introduced.
|
  |
10:15 - 10:40 |
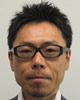 |
- Sponsor presentation
Simulation Strategy of Dassault Systems
- Mr. Koei Iwamoto
Director, SIMULIA Japan, Dassault Systemes K.K.
|
 |
Dassault Systems presents the latest simulation portfolio of SIMULIA brand of realistic simulation products and their future strategy of the simulation products. |
10:40 - 11:10 |
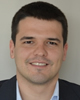 |
- Structural Optimization with SIMULIA TOSCA Structure 8.1
- Mr. Chavdar Georgiev
Technical Director, SIMULIA Optimization, Dassault Systemes
|
 |
Demands on state-of-the-art products are stronger than ever. Leading companies are subject to accelerating changes in production and development and increasing global competition. The latest release of SIMULIA Tosca Structure provides a highly effective market-leading technology for rapid and reliable design of lightweight, rigid, and durable components and systems. |
11:10 - 11:40 |
- Introduction of the weight reduction consulting service utilizing non parametric optimization
- Yusuke Houki, Structure Performance Optimization Group, Engineering Department 1, VINAS Co., Ltd.
- We have utilized non parametric optimization technology for weight saving design for a long time, and have provided design consulting service in fields such as domestic cars, heavy industry, industrial machine, etc.
In this session, we will introduce applied examples and our structural design optimization consulting services in Japan.
|
  |
11:40 - 12:10 |
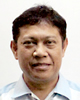 |
- Application of non-parametric optimization technology in weight reduction of a knuckle used in a car
- Dr. Anang Cakrawala
Casting Technology Development Dept. Technologies Management Div., RIKEN CORPORATION
|
   |
In today’s competitive global market, automotive component makers have to satisfy customers requiring faster lead-time and lighter component designs. In order to cope with the situation, we chose to use non-parametric optimization technology linked with CAE. We introduced the technology successfully by using VINAS’s consultation for weight reduction. Example results will be presented. |
12:10 - 13:30 |
Lunch / Demonstration *Short presentation |
13:30 - 13:55 |
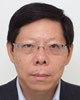 |
- Sponsor presentation
New Development of Multidisciplinary Analysis Solver MSC Nastran - MSC Nastran Embedded Fatigue Analysis Solution -
- Mr. Gaowen YE
Director, MSC Nastran Business Development, MSC Software Ltd.
|
 |
MSC Nastran has been evolved into a multi-disciplinary analysis platform by integrating many advanced analysis technologies in order to satisfy various analysis needs of engineering product/system design. In order to drastically improve the current CAE based fatigue analysis process, MSC Nastran Embedded Fatigue (NEF) analysis solution has been newly developed. In this presentation, this solver embedded fatigue analysis solution will be presented along with real application examples. |
13:55 - 14:15 |
- Introducing the latest version of the Large-scale CAD data conversion repair tool TransMagic R11
- Takao Minemura, Structure Performance Optimization Group, Engineering Department 1, VINAS Co., Ltd.
- “MagicHeal”the new module of TransMagic R11 has reinforced its CAD data repair, analysis, and editing features, and has made it easier to use for CAE-CFD. This session will introduce the main features and new functionalities of TransMagic R11.
|
       |
14:15 - 14:40 |
- Phoenix V11.2 and Product Development Plan
- Nobuyuki Suzuki, Phoenix Group, Project Development Department, VINAS Co., Ltd.
- Introducing new functions for "Phoenix V11.2" and the new packaging "ModelCenter Desktop" to build/execute workflow for analysis engineers, along with “ModelCenter Server” used for Simulation Data Management and executing workflow through Web interface by Designers.
|
 |
14:40 - 15:20 |
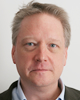 |
- Deploying Phoenix Integration Tools to Benefit the Entire Engineering Organization
- Scott Ragon, Ph.D.
Director, Technical Business Development, Phoenix Integration
|
 |
ModelCenter Desktop makes it easy for engineers to integrate their simulation tools together and to create and automate engineering workflows. Engineers in a wide variety of different industries (aerospace, automotive, shipbuilding, steel manufacturing, etc.) use ModelCenter Desktop to improve the efficiency of their design process and find better designs. A number of engineering organizations are achieving further benefits by sharing these reusable engineering workflows in an easy to use and consistent format with others in their organization - production engineers, managers, and even their sales teams. This presentation will discuss ways in which Phoenix Integration tools (ModelCenter Desktop and ModelCenter Server) can be deployed to benefit the entire engineering organization and beyond. Several customer case studies will be presented. |
15:20 – 15:35 |
Coffee Break/Demonstration *Short presentation |
15:35 - 16:15 |
- Phoenix Customer Examples
- Scott Ragon, Ph.D.
Director, Technical Business Development, Phoenix Integration
- Several different case studies and customer examples will be presented. Customers will include Lockheed Martin, NASA Jet Propulsion Laboratories, Aerolia, and Airbus. Applications will include workflow automation, model based systems engineering, and engineering data management.
|
      |
16:15 - 16:45 |
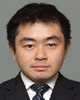 |
- Launch Vehicles flight path evaluation and system design using Phoenix Suite
- Mr. Toshiaki Daibo
Associate Senior Engineer, Space Transportation System Research and Development Center, Japan Aerospace Exploration Agency (JAXA)
|
 |
At JAXA, we develop various types of evaluation analysis tools for flight planning of Launch Vehicles and incorporate them with Phoenix Suite, so that they can be efficiently used by launchers' suppliers. In addition, various R&D projects and safety evaluation analyses performed by JAXA will be presented. |
16:45 - 17:25 |
 |
- Special Speech
Innovation of system development methodology that is happening worldwide.
- Associate Professor Seiko Shirasaka
Graduate School of System Design and Management, KEIO University
|
 |
Approach of system development is beginning to change significantly worldwide. In this presentation, introduce the latest trends in MBSE and System Engineering as a system development methodology perspective. |
17:25 - 17:30 |
Break |
(Broadcasting) Keynote Speech |
17:30 – 18:30 |
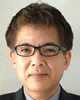 |
- Management of technologies and value creation in manufacturing industries:Importance of core technologies and non-functional premium values
- Professor Kentaro Nobeoka
Director, Institute of Innovation Research, Hitotsubashi University
|
|
Nowadays, it is difficult to create values leading to profits by only excelling in manufacturing. In order to create values, it is important to establish unique core technologies that cannot be imitated and to achieve truly high values for customers (non-functional premium values). |
Reception Party |
18:30 – 20:30 |
- A fantastic opportunity for sharing and exchanging information with each other.
- - Venue: Tokyo Conference Center Shinagawa - 5th floor foyer [in front of the grand hall] -
※Please notify your attendance at the time of registration. |
-Please note the program may change without prior notice.
-Company and product names are trademarks or registered trademarks.
 |
9:00 – 9:30 |
Registration |
9:30 - 10:00 |
- Opening Speech
New style of designing based on use of cloud service
- Yasuhiko Fujikawa, President & CEO, VINAS Co., Ltd.
|
|
10:00 - 10:15 |
- An effective post processing method using FieldView 14 in a cloud computing environment
- Yoshiyuki Sawa, Pre & Post Technical Group, Engineering Department 1, VINAS Co., Ltd.
- FieldView 14 is newly equipped with functions such as the improvement of spray visualization and multi window display for dataset comparison which allows an even greater reduction for the post-processing workload. Effective Post processing methods using FieldView in cloud-computing environments such as workflow construction for mid to large-scale analysis data parallel visualization process will be introduced.
|
 |
10:15 - 10:55 |
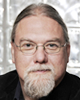 |
- FieldView and Fluid Dynamics: From 1991 to 2035
- Mr. Steve M. Legensky
Founder and General Manager, Intelligent Light
|
 |
FieldView was first introduced when the Cray 2 was a top supercomputer and two million cells was a huge CFD case. We’ll travel from these early days into the future from the perspective of computing, visualization and data management. |
10:55 - 11:35 |
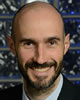 |
- Pushing the Limits of CFD Post-processing in the Auto Industry
- Mr. Yves-Marie Lefebvre
FieldView Product Chief, Intelligent Light
|
 |
Although working in a highly constrained environment, automotive engineers keep pushing the limits of CFD with increasingly complex simulations. Through three industrial examples, we will review how FieldView’s technology is helping do more with the same hardware, whether that's getting post-processing results faster or being able to interact with large transient results as never before. |
11:35 - 12:05 |
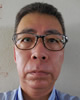 |
- Current issues and future prospects in processing of results of automotive aerodynamic analyses
- Mr. Yoshimitsu Hashizume
Group Manager, Aerodynamics & Aeroacoustics Group, SUZUKI MOTOR CORPORATION
|
     |
In response to demands for higher accuracy of aerodynamic analyses of automobiles, calculations involving several hundred million to several billion grid points are being performed. Furthermore, these are unsteady analysis calculations and their result data measure up to some terabytes. The processing of such large scale result data will be discussed.
|
12:05 - 13:25 |
Lunch / Demonstration *Short presentation |
13:25 - 13:40 |
- Introduction of Pointwise V17.2 and High Fidelity Mesh Generation Consulting Service by VINAS
- Hiroyuki Suzuki, Pre & Post Technical Group, Engineering Department 1, VINAS Co., Ltd.
- Pointwise V17.2 and new T-REX technology enables to generate hexahedral cells automatically for boundary layer, which have made all engineers nervous to assemble structured grid. The new features of the latest version of Pointwise will be presented. In addition, VINAS’s mesh generation consulting service for high fidelity CFD simulation that is based on over 17 years of experience will be introduced.
|
 |
13:40 - 14:20 |
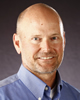 |
- Expanded Meshing Flexibility for Higher Fidelity Simulations
- Dr. Richard J. Matus
Vice-President, Sales & Marketing, Pointwise, Inc.
|
 |
The variety of meshes Pointwise creates continues to expand with the new unstructured hexahedral extrusion and upcoming overset grid assembly techniques. These methods will be described along with examples of their use and how they integrate with other Pointwise features. |
14:20 - 15:00 |
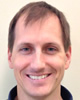 |
- The challenges of spacecraft launch abort aerodynamic analysis
- Mr. Darby J. Vicker
Aerospace Engineer, Applied Aeroscience and CFD Branch, National Aeronautics and Space Administration (NASA)
|
 |
The analysis of a spacecraft launch abort system poses many challenges that are difficult to model computationally. Additionally, the sheer size of the abort parameter space makes it difficult to fully characterize the aerodynamics. Examples from recent experience will be presented. |
15:00 – 15:15 |
Coffee Break/Demonstration *Short presentation |
15:15 - 15:45 |
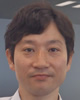 |
- Use of HPC and large-scale analyses in plant engineering
- Mr. Kyoji Ishikawa
Advanced Process Engineering Unit, CHIYODA CORPORATION
|
     |
In plant engineering, technological breakthroughs are being brought about by large-scale and high-accuracy analyses enabled by use of HPCs. Examples of large-scale analyses of chemical and LNG plants will be presented.
|
15:45 - 16:15 |
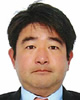 |
- Development of an Alternative Technology to the Towing Tank Test by Quasi-direct Numerical Simulation
- Tatsuo Nishikawa, Dr. Eng.
Manager, Design System Development Section, Marine Technology & Development Department, The Shipbuilding Research Centre of Japan
|
   |
This presentation gives an overview of the world’s first practical applications of the fully-resolved Large Eddy Simulation on a whole ship hydrodynamics with tens of billion cells computational grid. It includes some details about our survey into the possibility of using T-Rex anisotropic hexa-mesh generation function of Gridgen for this type of calculation. |
16:15 - 16:45 |
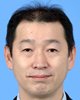 |
- Development of “LPTlib” – a large-scale parallel particle calculation library
- Dr. Kenji Ono
Team Leader, Advanced Visualization Research Team, Advanced Institute for Computational Science(AICS), RIKEN
|
    |
We are developing a particle tracking algorithm which is scalable and is used together with parallel fluid analysis calculation of a domain decomposition type. By implementing near-perfect load balancing and communication overlapping, this algorithm is expected to achieve excellent scalability. An overview of the algorithm and examples of calculation results will be presented.
|
16:45 - 17:25 |
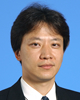 |
- Special Speech
Industrial application of large-scale fluid analysis – Current status and future prospects
- Professor Chisachi Kato
Institute of Industrial Science, The University of Tokyo
|
   |
Performance of supercomputers is remarkably improving and it is expected that in several years, petaflop class computers will become available for large-scale calculations in industries. The presentation includes the latest results of large-scale LES analyses and what is expected in the future. |
17:25 - 17:30 |
Break |
Keynote Speech |
17:30 – 18:30 |
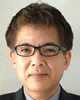 |
- Management of technologies and value creation in manufacturing industries:Importance of core technologies and non-functional premium values
- Professor Kentaro Nobeoka
Director, Institute of Innovation Research, Hitotsubashi University
|
|
Nowadays, it is difficult to create values leading to profits by only excelling in manufacturing. In order to create values, it is important to establish unique core technologies that cannot be imitated and to achieve truly high values for customers (non-functional premium values). |
Reception Party |
18:30 – 20:30 |
- A fantastic opportunity for sharing and exchanging information with each other.
- - Venue: Tokyo Conference Center Shinagawa - 5th floor foyer [in front of the grand hall] -
※Please notify your attendance at the time of registration. |
-Please note the program may change without prior notice.
-Company and product names are trademarks or registered trademarks.