 |
9:00 – 9:30 |
Registration |
9:30 - 10:00 |
- (Broadcasting)
Advanced design style in the age of cloud computing
- Yasuhiko Fujikawa, President & CEO, VINAS Co., Ltd.
- For R&D divisions that uses CAE/CFD to improve product performance, it has been a universal theme to be able to realize high predictability at low cost and in shorter time. However in recent years, with the cost decrease for cluster servers and the spreading of cloud computers, we are now given a wide range of choices for HPC calculation infrastructure. In addition, it has become possible to conduct your regular analysis or high-accuracy analysis efficiently by selecting out the most purpose-fitted software from a variety of opensource codes and high-performance commercial softwares.
In our opening session, will will report on our latest corporate activities and also talk about the advantages and tips of using cloud computers and opensource codes for your daily designing work.
|
10:00 – 10:15 |
- To achieve weight reduction and increase reliability by TOSCA
- Hidetoshi Takaoka, Manager, Engineering Department 3, VINAS Co., Ltd.
- For weight reduction and increasing reliability, it is very important to use optimization tools in a design process.
In this session, we will introduce the structural optimization system TOSCA and our structural optimization consulting services by our engineers from automobile and aircraft manufacturers.
|
 |
10:15 – 10:55 |
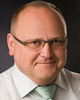 |
- Global Trends in Optimization Technology
- Mr. Henning STAUFENBERG, Director International Business Development, FE-DESIGN
|
 |
Given the global challenges in today’s highly competitive market places the major players in each industry segment, especially in automotive, have to ensure that their product development processes are fast, reliable and innovative. Key success factors for achieving this are the introduction of optimization and process automation technologies. The TOSCA product line of FE-DESIGN is now after being integrated into the DS SIMULIA product portfolio part of the most complete optimization environment in the market. |
10:55 – 11:35 |
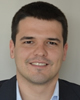 |
- Overview of New Functionalities in the Latest TOSCA Structure Version
- Mr. Chavdar Georgiev, Director Technical Sales, FE-DESIGN
|
 |
The increasing global competition requires that leading companies use the best technology to keep their market position. Demands on production and development are stronger than ever. FE-DESIGN introduces with the latest release of TOSCA Structure a highly effective market-leading technology for rapid and reliable design of lightweight, rigid, and durable components and systems. |
11:35 – 12:05 |
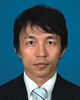 |
- Optimization of railway vehicle structure using TOSCA
- Mr. Masakazu Takagaki, Ph.D., Laboratory Head, Track Dynamics Division, Computational Mechanics, Railway Technical Research Institute
|
  |
Recently, railway vehicle structures need to be considered from the viewpoints of both strength enhancement and weight reduction, because they tend to be heavy due to additional equipment for enhanced safety and amenity while energy saving is required at the same time. By using TOSCA, optimization studies have been conducted on vehicle structures and some example of them will be presented in this session. |
12:05 - 13:25 |
Lunch / Demonstration *Short presentation |
13:25 – 13:55 |
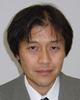 |
- Optimization of attachment structure of vehicle towing device
- Mr. Takashi Morita, Chief Engineer, Department 5, Technology Development Division 11, Automobile R&D Center, Honda R&D Co., Ltd.
|
   |
Areas in the rear of an automobile body near the towing device attachment point are mainly constructed of thin plates. An example of attempt to reduce weight while satisfying required strength performance by using TOSCA.bead will be presented. |
13:55 – 14:35 |
|
- Structural Analysis and Design Using ModelCenter: Recent Customer Examples
- Scott Ragon, Ph.D., Director Research, Phoenix Integration, Inc.
|
 |
After a brief introduction to the Phoenix Integration product line, several recent structural analysis and design examples will be discussed. Applications will include both aircraft structures and building design. Technologies that will be highlighted will include workflow automation, response surface modeling, design of experiments, optimization, reliability analysis, and cloud computing. |
14:35 – 14:50 |
Coffee Break/Demonstration |
14:50 – 15:05 |
- Introduction of the latest Version of TransMagic R10
- Tos Sugino, Director, Marketing Department, VINAS Co., Ltd.
- GUI localization in Japanese of TransMagic R10 provides easy operation to repair gaps and defects on 3D surface models and data exchanges between 3D CAD systems. MagicCheck is released in R10 to compare and validate 3D geometry. This session will introduce main feature and new functionalities of TransMAgic R10.
|
 |
15:05 – 15:45 |
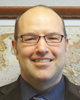 |
- A Better Way to Translate, Repair, Compare, and Validate CAD Data
- Mr. Craig Dennis, Founder & CTO, TransMagic, Inc.
|
 |
Most manufacturers use multiple CAD systems, and all exchange data with their suppliers. The resulting inaccurate CAD data is a billion dollar problem. TransMagic creates native-kernel, best-in-class tools for translating, repairing, comparing, and validating CAD data. |
15:45 – 16:00 |
- Outline of OOFELIE::Multiphysics, the strong coupling simulation system for industry designers
- Hidetoshi Takaoka, Manager, Engineering Department 3, VINAS Co., Ltd.
- The outline of OOFELIE::Multiphysics which can simulate the strong coupling behavior between structure, thermal, electric, fluid and so on, will be presented. The functionalities for MEMS device simulation, and the case studies of thermo-mechanical simulation and fluid structure interaction simulation will be also provided.
|
 |
16:00 – 16:40 |
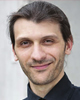 |
- OOFELIE::Multiphysics for Robust Micro Systems Design
- Mr. Pascal De Vincenzo, General Manager, OPEN ENGINEERING
|
 |
OOFELIE::Multiphysics, the numerical simulation solution developed and commercialized by Open Engineering is used by industrials to predict the behavior of their micro systems. In the framework of this presentation, the modeling of recent MEMS applications for the automotive market will be presented. |
16:40 – 17:20 |
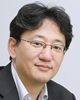 |
- Micro optical application of static-driven MEMS micro actuator
- Professor Hiroshi Toshiyoshi, Research Center for Advanced Science and Technology (RCAST), The University of Tokyo
|
 |
Micro Electro Mechanical Systems (MEMS) refers to the design and manufacturing technology of microscopic electro mechanical systems manufactured by applying micro fabrication technology for semiconductors. This presentation introduces devices designed by using OOFELIE, including a static-driven MEMS optical fiber switch, a scanner for an image display, a shutter for a spectroscope, and so on. |
17:20 – 17:30 |
Break |
(Broadcasting) Keynote Speech |
17:30 – 18:30 |
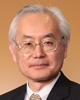 |
- K-computer and its industrial use
- Mr. Satoshi Itoh,Dr.Eng., Coordinator, Advanced Institute for Computational Science(AICS), RIKEN
|
|
This presentation outlines the K-computer, one of the highest-performing supercomputers in the world and takes a look at examples of its use, mainly in the industrial field. In addition, future plans of the K-computer and requirements for industrial use will be discussed. |
Reception Party |
18:30 – 20:30 |
- Please join! This is a good opportunity for sharing and exchanging information with each other.
- - Venue: Tokyo Conference Center Shinagawa - 5th floor foyer [in front of the grand hall] -
*Please notify your attendance at the time of registration.
|
-Please note the program may change without prior notice.
-Company and product names are trademarks or registered trademarks.
 |
9:00 – 9:30 |
Registration |
9:30 - 10:00 |
- Advanced design style in the age of cloud computing
- Yasuhiko Fujikawa, President & CEO, VINAS Co., Ltd.
|
10:00 - 10:15 |
- Introduction of FieldView V14 to realize the high-speed particle visualization and multi-window display
- Shinya Higaki, CFD Product Group, Engineering Department 1, VINAS Co., Ltd.
- Many new features will be added in the next version V14 FieldView. It makes it possible for multi-window display function, display is performed at the same time multi-faceted.
In addition, new vector display function , high-speed of the particles display speed will improved.
In this seminar, We will introduce the efficient method for visualization by FieldView V14. |
 |
10:15 - 10:55 |
 |
- Engineered CFD Workflows for Effective HPC Performance
- Mr. Steve M. Legensky, Founder and General Manager, Intelligent Light
|
 |
As core counts increase, CFD users are expecting more throughput for simulations. However, many companies experience bottlenecks due to legacy workflows from older computing and data flow styles. We describe how new, engineered workflows produce higher throughput without increasing hardware costs. |
10:55 - 11:35 |
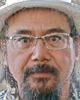 |
- Analysis of Extreme Scale CFD Engineering Applications
- Dr. Earl P.N. Duque, Manager of Applied Research, Intelligent Light
|
  |
Extremely large CFD simulations require parallel and batch post-processing capabilities such as those available in FieldView. Two recent projects, analysis of a high lift transport aircraft and a wind farm simulation with 10’s of billions of grid points will be presented. |
11:35 - 12:15 |
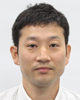 |
- Application of cloud technology in engineering and a case example
- Mr. Kyoji Ishikawa, Engineering Solution Unit, CHIYODA CORPORATION
|
   |
This presentation discusses use of HPC computers (cloud) in the engineering field including plant construction and touches upon existing issues. An example of study conducted by using a large-scale model of industrial plant will be presented. |
12:15 - 13:35 |
Lunch / Demonstration *Short presentation |
13:35 - 13:50 |
- Pointwise V17.1 – Advancing Front Meshing and T-REX for High-Quality Unstructured Mesh Generation
- Masanori Hashimoto, CFD Product Group, Engineering Department 1, VINAS Co., Ltd.
- The latest version of Pointwise V17.1 has included great features such as Advancing Front Meshing, T-REX and so on. With these new features, high-quality mesh can be generated more robustly with saving your time. This presentation will provide an overview of Pointwise V17.1 and Case Studies of Advancing Front Meshing.
|
 |
13:50 - 14:30 |
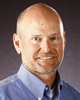 |
- Efficiently Managing CAE Workflows with Pointwise
- Dr. Richard J. Matus, Vice-President, Sales & Marketing, Pointwise, Inc.
|
 |
Pointwise famously generates high-quality meshes, but another of its strengths is the ability to integrate into any CAE workflow. The presentation will highlight the various ways people use Pointwise as an integral part of their analysis process. |
14:30 - 15:10 |
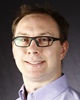 |
- Predicting Infrared Signature and Susceptibility with Pointwise and ShipIR/NTCS”)
- Mr. Chris Sideroff, PhD, Senior Research Engineer, W.R. Davis Engineering
|
  |
ShipIR/NTCS is a comprehensive software engineering tool for predicting the thermal infrared (IR) signature and IR susceptibility of naval warships and aircraft. Pointwise has been incorporated into the ShipIR/NTCS analysis process to decrease platform modeling efforts and to enable coupling between ShipIR and CFD (ANSYS Fluent). |
15:10 – 15:25 |
Coffee Break/Demonstration *Short presentation |
15:25 - 15:55 |
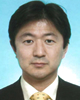 |
- Development of numerical analysis technology for technological advancement of coal-fired power generation
- Mr. Hiroaki Watanabe, Ph.D., Senior Research Scientist, Energy Engineering Research Laboratory, Central Research Institute of Electric Power Industry
|
   |
Coal-fired power generation is drawing attention in Japan from the viewpoint of reducing cost and sourcing risks of fuels and ensuring a stable power supply for the whole nation. Studies aimed at diversification of fuels for coal-fired power generation and reduction of environmentally harmful emissions will be presented in this session. |
15:55 - 16:35 |
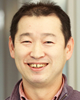 |
- Development of ubiquitous application for design process
- Dr. Kenji Ono, Team Leader, Advanced Visualization Research Team, Advanced Institute for Computational Science(AICS), RIKEN
|
  |
This presentation discusses application development of a CAE system which assists quick decision making in design process by using various computing resources such as PCs, private/public cloud, and super-computers. |
16:35 – 17:15 |
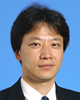 |
- Special Speech
Latest achievement of large-scale practical-use computation by FrontFlow/blue
- Professor Chisachi Kato, Institute of Industrial Science, The University of Tokyo
|
 
|
FrontFlow/blue (FFB) is a general purpose CFD solver based on finite element method with high parallelization efficiency and computational accuracy, and supports parallel computation using tens of thousands of cores. This presentation shows the latest achievement of practical-use computation by FFB using K-computer and FX-10. |
17:15 – 17:30 |
Break |
Keynote Speech |
17:30 – 18:30 |
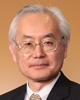 |
- K-computer and its industrial use
- Mr. Satoshi Itoh,Dr.Eng., Coordinator, Advanced Institute for Computational Science(AICS), RIKEN
|
|
This presentation outlines the K-computer, one of the highest-performing supercomputers in the world and takes a look at examples of its use, mainly in the industrial field. In addition, future plans of the K-computer and requirements for industrial use will be discussed. |
Reception Party |
18:30 – 20:30 |
- Please join! This is a good opportunity for sharing and exchanging information with each other.
- - Venue: Tokyo Conference Center Shinagawa - 5th floor foyer [in front of the grand hall] -
*Please notify your attendance at the time of registration.
|
-Please note the program may change without prior notice.
-Company and product names are trademarks or registered trademarks.