DAY 1:Post-processor & Automotive, Urban Development and Medical |
13:00 - 13:20 |
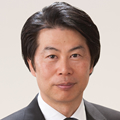 |
- Opening
- Yasuhiko Fujikawa, President & CEO, VINAS Co., Ltd
|
13:20 - 14:00 |
基調講演 |
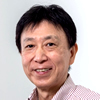 |
- One View of Recent Data Analysis under the Transition of CFD Simulations in Industries
- Professor Kozo Fujii, Department of Information and Computer Technology, Tokyo University of Science
- Post processing is becoming a main part of CFD simulations under the rapid progress of computer hardware and application software.
This lecture flashes back the history of post processing of CFD and considers transition of data analysis with traditional and new data science technologies.
|
|
14:00 - 14:15 |
- FieldView 19とハイブリッドパラレルによる大規模CFD解析の効率化
- Hiroyuki Suzuki, Engineering Department 1, VINAS Co., Ltd.
|
|
14:15 - 14:45 |
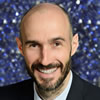 |
- 20th FieldView Release: Still Pushing the Limits for You.
- Mr. Yves-Marie Lefebvre, FieldView Business Director FieldView CFD Inc.
- Building on many years of fast, reliable, high-quality CFD post-processing, FieldView 20 will once again push the limits to help you get your work done faster. With hybrid parallelism and by moving more operations to the GPU, FieldView 20 will let you do more with the same hardware. It will also deliver a number of customer requested features, that will be introduced in this presentation and demonstrated with real applications from various industries.
|
|
14:45 - 15:15 |
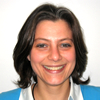  |
- The key role of an efficient post-processing with FieldView in the Dallara CFD Process
- Simona Invernizzi, CFD Manager, CFD Department, Dallara Automobili SpA
Elisa Serioli, CFD Methodologist, CFD Department, Dallara Automobili SpA
- Nowadays the CFD simulation is an essential tool since the supporting information and awareness provided for a state-of-art aerodynamic development of a racing car. In this respect Dallara, a Company located in the Parma area and working in Motorsport and Automotive services, invested a lot in the simulation tools (hardware and software) in order to get the maximum benefit in optimizing different products. In particular, for the CFD tool, it is fundamental to speed up every phase of the CFD process in order to get the most accurate results in the shorter time and, moreover, deriving the most useful information from the amount of data generated, this for sure through smart and efficient post-processing. In this context we will present the role of the FieldView tool in achieving the target of the process speed up and managing the most significant information coming from the CFD simulation.
|
|
15:15 - 15:25 |
Break |
15:25 - 15:40 |
- HELYXとHELYX-Adjointによる流体機械のトポロジ最適化とクラウド環境における大規模流体解析
- Yoshiyuki Sawa, Engineering Department 1, VINAS Co., Ltd.
|
|
15:40 - 16:10 |
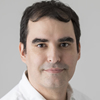 |
- HELYX: New Features and Enhancement in Version 3.3.0
- Mr. Francisco J. Campos, MSc DIC, Director of Operations, ENGYS Ltd.
- In this presentation we introduce the new features and latest CFD technologies developed by ENGYS as part of the latest version of HELYX 3.3.0, including a new interface for Generalised Internal Boundaries (GIB) and a brand new block-coupled solver framework for both incompressible and compressible flows.
|
|
16:10 - 16:40 |
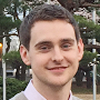 |
- Surrogate-modelling the effect of building shape on the local wind microclimate through multi-directional, multi-fidelity CFD
- Aidan McLoughlin , CFD Engineer: WSP in the UK
- ビル風が歩行者に与える影響は居住性や快適性、安全性を考慮するうえで大きな要因となり、建物の周辺で想定される風によっては建設が許可されない可能性もあります。CFDではこのモデル化が重要になります。
WSP社では、主にCFDと風洞実験を組み合わせた「トータル・ウィンド・エンジニアリング」フレームワークを構築することにより、HELYXを活用して快適な街づくりと設計期間の短縮を実現しています。本セッションでは、日本の新潟市の高層ビルと周辺建築物をモデル化して、HELYX v3.2.0のRANSとHybrid RANS-LESによるCFD結果と観測データから歩行者に与える影響や快適性を検討した結果について紹介します。 |
|
16:40 - 17:10 |
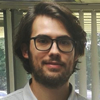 |
- Formation of Vortices in Idealised Branching Vessels: A Parametric Validation Study with HELYX and Dakota
- Rudolf Hellmuth , Vascular Flow Technologies in the UK
- Atherosclerosis, the leading causes of death in the developed world, preferentially occurs near the junction of branching vessel, where blood recirculation tends to occur. Studies have shown that the endothelial cells covering the inside of blood vessels develop an atherogenic phenotype when exposed to low wall shear stress in recirculation zones. In 1980, Karino and Goldsmith mapped the the formation of eddies in glass models of circular branching junctions of various branching angles, diameter ratios, and Reynolds numbers (up to 350). These models served as idealized models of branching blood vessels in mammalian circulatory systems.
For decades, CFD has been used to predict flow patterns such as separation and recirculation zones in hemodynamic models, but those predictions have rarely been validated with experimental data. Recently, a technical standard was issued by the American Society of Mechanical Engineers to guide the execution of verification and validation (V&V) procedures to demonstrate credibility and fidelity of computational models in the medical device industry (ASME V V 40 - 2018). In the context of V&V, we set a parametric setup using Dakota to automatically run more than 12,000 CFD simulations using HELYX, where the whole range of parameters of the experiment of Karino and Goldsmith (1980) were covered. The critical Reynolds number for both the formation of the main vortex (MV), in the main branch, and side vortex (SV), in the side branch, was automatically detected and saved into a a table data. Therefore, it was shown that HELYX is able to correctly predict the critical Reynolds of vortices, which validates the use of this CFD package to predict the same kind of vortices in patient-specific branching blood vessels.
|
|
17:10 - 17:40 |
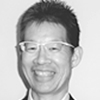 |
- Transformation of Fluid Analysis using HELYX add-on and Built-in Template in AISIN AW Co., Ltd
- Mr. Takeshi Yamaguchi, Doctor of Engineering Chief Research Engineer, Engineering Division, AISIN AW CO., LTD.
- The example of the application of HELYX add-on features such as HYLYX-Coupled and HELYX-Adjoint to our Automatic Transmission product will be introduced.
|
|
Please note the program may change without prior notice.
-Company and product names are trademarks or registered trademarks.
DAY2:Pre-processor & Turbo Machinery, Aerospace and Automotive |
13:00 - 13:15 |
- サーフェスメッシュ生成機能を強化したPointwise V18.4の最新情報とヴァイナスのテクニカルサポート・コンサルティングサービス
- Shunsuke Otsubo, Engineering Department 1, VINAS Co., Ltd.
|
|
13:15 - 13:45 |
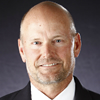 |
- Increasing Automation in the CFD Mesh Generation Process
- Richard J Matus, Ph.D. Executive Vice-President, Pointwise, Inc.
- Pointwise is known for providing explicit meshing control and the flexibility to easily integrate into customers’ design and analysis processes resulting in highly efficient and accurate CFD simulations. Recent developments have focused on automating the meshing process to achieve both precise meshing and ease-of-use. Details of new features like voxels and automatic surface meshing as well as upcoming automation-directed developments will be shown. The benefits of these approaches will be illustrated with example application and benchmark cases. A product roadmap will show Pointwise’s future direction toward making fully automatic, high quality meshing invisible to the user.
|
|
13:45 - 14:15 |
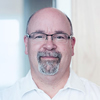 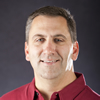 |
- Robust, Efficient and Accurate Mesh Adaptation for Turbomachinery CFD Simulations
- Paul Galpin, Director, ISimQ
Nick Wyman, Director, Applied Research, Pointwise, Inc.
- Paul Galpin of ISimQ and Nick Wyman of Pointwise, discuss solver-independent assessment of interpolation error using Pointwise mesh adaptation. Additionally, they will show the control of mesh size via mesh complexity. There will be a discussion of the following key results.
•Systematic reduction of numerical error
•Adaptation maintains geometry associativity
•Mesh quality maintained and often improved
•No additional cost compared with fixed mesh
|
|
14:15 - 14:45 |
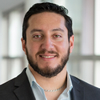 |
- Understanding Tractor Trailer Aerodynamics Using a Time Accurate Approach
- David E. Manosalvas-Kjono, PhD , Co-founder and CEO : Aeromutable Corporation
- David Manosalvas-Kjono of Aeromutable Corporation shows how SU2 was used for a transient simulation conducted to capture near body drag and wake drag phenomena with a Delayed Detached Eddy model based on the Shear Stress Transport turbulence. The control over mesh topology and boundary layer generation within Pointwise provided a mesh best suited for this simulation.
|
|
14:45 - 15:15 |
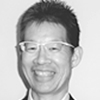 |
- Auto-meshing System for Torque Converter Model
- Mr. Takeshi Yamaguchi, Doctor of Engineering Chief Research Engineer, Engineering Division, AISIN AW CO., LTD.
- With a new designated GUI, auto-meshing system for torque converter model using Pointwise/Gridgen was developed. The example of how time consumption for meshing is dramatically reduced by using this system will be introduced.
|
|
15:15 - 15:25 |
Break |
15:25 - 15:40 |
- VFBasisによる流体振動・騒音解析と適用事例
- Yoshiyuki Sawa, Engineering Department 1, VINAS Co., Ltd.
|
|
15:40 - 16:10 |
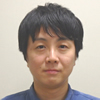 |
- Applications of FBasis to unsteady fluid datasets
- Mr. Yuya Omichi, Doctor of Engineering Research Engineer, Research and Development Directorate, Japan Aerospace Exploration Agency
- The Japan Aerospace Exploration Agency (JAXA) is developing a method for identifying flow patterns based on modal decompositions, which enables us to easily and quickly extract knowledge from unsteady fluid datasets obtained from CFD and wind tunnel experiments. We also provide the developed methods as a software, FBasis. In this presentation, I will introduce the usage and effectiveness of FBasis through examples of application to practical fluid datasets.
|
|
16:10 - 16:25 |
- 圧縮性流体・マルチフィジクス対応ソルバCRUNCH CFD V3.3ご紹介
- Akio Kawaguchi, Engineering Department 3, VINAS Co., Ltd.
|
|
16:25 - 17:05 |
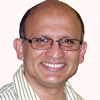 |
- High-Fidelity Modeling of sCO2 Cycle Components: Compressors and Direct-Fired Combustors
- Ashvin Hosangadi, Ph.D. , Vice-President , CRAFT Tech.
- This presentation will focus on technical issues and simulation challenges in modeling sCO2 compressors and oxy-combustors for direct fired cycles at off-design conditions. The CRUNCH CFD® framework features advanced capabilities for modeling subcritical operation of sCO2 compressors and has been extensively validated. Results for subcritical operation of the Sandia compressor will be presented. Oxy-combustors in direct fired sCO2 cycles operate at high pressures (~300 bar) with large amounts of CO2 recycled as diluent to achieve a low exit temperature (~1150 K). There is a large design space for optimally splitting the CO2 between the injector and chamber wall for cooling. A comprehensive modeling framework for high-fidelity design support is presented and physics affecting flame stability and combustor performance are identified.
|
|
17:05 - 17:35 |
 |
- Liquid Rocket Engine Simulation Technology by using CRUNCH CFD
- Mr. Hideo Negishi, Chief Research Engineer, Research and Development Directorate, Research Unit III, Japan Aerospace Exploration Agenc
- Japan Aerospace Exploration Agency (JAXA) has been using CRUNCH CFD in developing the first-stage engine LE-9 for Japan's new flagship launch vehicle ”H3”.
As the inside of the Liquid Rocket Engine is multi-physics environment involving real fluid physical properties, heat transfer, combustion and phase change, etc. under wide range of pressure and temperature conditions, it is very complicated to handle with conventional CFD solvers. In this talk lecture, the example of the initiative development of the simulation technology in cooperation with the software developer, CRAFT Tech, for the past 10 years will be introduced.
|
|
Please note the program may change without prior notice.
-Company and product names are trademarks or registered trademarks.
DAY3:Optimization Design & HPC |
13:00 - 13:40 |
Opening Special Lecture |
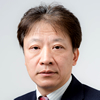 |
- Large-Scale Fluid Computation and Optimization Design in the era of "FUGAKU"
- Professor Chisachi Kato, Institute of Industrial Science, The University of Tokyo
- The next flagship supercomputer called "FUGAKU" has been smoothly prepared and adjusted. Starting from October this year, "Early Stage Utilization Task" is to be launched to achieve the early stage result. Full-scale operation is intended to be starting in early next year. By using new generation HPC like "FUGAKU", it also has been confirmed that the applications can be executed with high speed over several tens of times faster than the era of "K" supercomputer. In this lecture, the example of fan optimization design using the state of the art of HPC is to be observed.
|
|
13:40 - 13:55 |
- 多目的最適化アルゴリズム「CHEETAH」を統合した、最新バージョンSculptor V4.0の新機能紹介と適用分野拡大に向けた取り組み
- Nobuyuki Suzuki, Engineering Department 2, VINAS Co., Ltd.
|
|
13:55 - 14:25 |
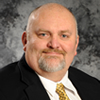 |
- Sculptor V3.9
New Features and Capabilities in Sculptor.
Shape Optimization of the Nacelles on a Business Jet.
- Mark D. Landon, Ph.D. Chief Technical Officer, Optimal Solutions Software, LLC
- An example of minimizing the drag on a business jet by shape optimization to reduce the shock just behind the leading edge on the upper surface of the nacelles will be presented. The Mesquite mesh smoothing tools have been incorporated into Sculptor. Even though Sculptor’s ASD provides very smooth volumetric morphing, mesh healing and smoothing functions are now available.
|
|
14:25 - 14:55 |
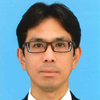 |
- SCULPTORを用いたポンプ形状最適化事例
- パナソニック エコシステムズ株式会社 R&D本部 熱・流体開発部 送風技術開発課 送風技術開発係
主務 重森 正宏 様
- ポンプ形状最適化にSCULPTORを適用した事例を紹介します。揚程、流量を最大化しながらトルクを最小化する形状を探索しました。メッシュモーフィングモデルを作成しパラメータスタディを行いました。クリギング法により応答曲面を作成して、最適形状を探索しました。
|
|
14:55 - 15:25 |
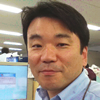 |
- 【協賛社発表】
富士通のスーパーコンピュータ PRIMEHPCシリーズのご紹介
- 富士通株式会社 プロセッサシステム事業本部 ソリューション開発統括部 アプリケーション技術部
シニアマネージャー 金澤 宏幸様
- 理化学研究所様と富士通が共同開発し、最新の性能ランキングで4冠を達成したスーパーコンピュータ「富岳」。「富岳」に採用したArm CPUであるA64FXを搭載し、高い電力当たり性能とスケーラビリティを実現するFUJITSU Supercomputer PRIMEHPC FX1000、ならびに、同様にA64FXを搭載し、空冷方式を採用した導入しやすいモデルであるFX700をご紹介いたします。
|
|
15:25 - 15:35 |
Break |
15:35- 16:05 |
- 【協賛社発表】
準最適メタスケジューラ (qopt-meta-sched)の紹介
- 公益財団法人 計算科学振興財団 研究部門 共用専門員 兼 主任研究員 博士(工学) 西川 武志 様
- 問題(サイズ、精度)と条件(速度優先、コスト抑制)に応じ計算資源を準最適選択し実行した結果を再学習して成長していく準最適メタスケジューラqopt-meta-schedを紹介する。
|
|
16:05 - 16:35 |
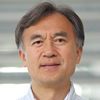 |
- 【協賛社発表】
SX-Aurora TSUBASAの最新情報とヴァイナス社との取り組みのご紹介
- 日本電気株式会社 AIプラットフォーム事業部 エキスパート 岩田 直樹 様
- PCIeカードに超高性能ベクトルプロセッサを搭載したSX-Aurora TSUBASAは従来のHPC領域の科学技術計算に加え、AI・ビッグデータ解析などの新しい領域でも活用できるようになりました。最新の活用事例をご紹介するとともに、SX-Aurora TSUBASA向けのSuper Matrix Solverのリリースなど、ヴァイナス社との取り組みについてご紹介します。
|
|
16:35 - 17:05 |
- HPCアプリケーション開発サービスとスパコンやクラウドコンピュータを効率的に利用するためのソリューションの紹介
- Kenji Morimoto, Project Development Department, VINAS Co., Ltd.
|
|
17:05 - 17:45 |
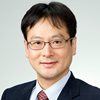 |
- New CAE by FUGAKU's Large-Scale Fluid Simulation and Data Science Fusion
- Professor Makoto Tsubokura, Center for Computational Science, RIKEN / Graduate School of System Informatics, Kobe University
- The simulation framework called "CUBE" using unified data structure based on hierarchical Cartesian grid for complex phenomenon coupled with fluid, structure, chemical reaction and sound etc. has been developed. The current situation of this development, especially tuning in "FUGAKU" and social contributions by "FUGAKU" is to be introduced. Moreover, the implementation of the data science and simulation on this framework to the new CAE will also be discussed.
|
|
17:45 - 17:55 |
- Closing Speech
- Yasuhiko Fujikawa, President & CEO, VINAS Co., Ltd
|
|
Please note the program may change without prior notice.
-Company and product names are trademarks or registered trademarks.