10:35 - 10:50 |
- Introduction of “FBasis” that is Proper Orthogonal Decomposition(POD), Dynamic Mode Decomposition (DMD) Analysis System based on machine learning method
- Akinori Shinohara, Applied Technology Department Manager, VINAS Co., Ltd.
- VINAS has been provided the solutions which improve the efficiency of CFD workflow at the wide range of manufacturing.
And FieldView, the solution of CFD post processing distributed by VINAS since 1996, has been applied to improve the product quality, reduce the manpower of CFD analysis, and also inherit the experience of expert engineer to the next generation.
FieldView 18 takes advantage of the latest high-speed graphic processing technology and allows laptop PCs to perform parallel processing of large-scale CFD analysis data.
This presentation gives examples of consultancy to improve and automate CFD design work including post processing.
|
|
10:50 - 11:00 |
Coffee Break |
11:00 - 11:30 |
- CFD post processing with FieldView 18 and construction of CFD workflow with VINAS
- Yoshiyuki Sawa, Engineering Department 1, VINAS Co., Ltd.
- VINAS has been provided the solutions which improve the efficiency of CFD workflow at the wide range of manufacturing.
And FieldView, the solution of CFD post processing distributed by VINAS since 1996, has been applied to improve the product quality, reduce the manpower of CFD analysis, and also inherit the experience of expert engineer to the next generation.
FieldView 18 takes advantage of the latest high-speed graphic processing technology and allows laptop PCs to perform parallel processing of large-scale CFD analysis data.
This presentation gives examples of consultancy to improve and automate CFD design work including post processing.
|
|
11:30 - 11:45 |
- Topology optimization for fluid machinery design
- Junichi Fukui Ph.D., HELYX Group, VINAS Co., Ltd.
- Topology optimization has a lot of flexibility for geometry change, and can search non-traditional optimized geometry of fluid channel. In this session it will show possibility for creating innovative fluid machinery design by CFD topology optimization software HELYX-Adjoint.
|
|
11:45 - 12:15 |
|
- It's being scheduled
|
|
12:15 - 13:25 |
Lunch & Demo |
13:25 - 14:00 |
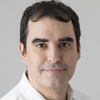 |
- New Features and Methods in HELYX 3.2.0
- Mr. Francisco Campos,
Director of Operations, ENGYS Ltd.
- In this presentation we introduce the new features and latest CFD technologies developed by ENGYS as part of HELYX 3.2.0.
|
|
14:00 - 14:15 |
- New features of Pointwise V18.3 and meshing consulting service by VINAS
- Shunsuke Otsubo, Engineering Department 1, VINAS Co., Ltd.
- The new version Pointwise V18.3 introduced unstructured mesh generation function “Hex Core” which can generate unstructured hexahedral cells. And also it introduced license-free viewer function that can display Pointwise mesh and utilize evaluation function. This presentation shows new features of the latest version of Pointwise V18.3 and meshing consulting service by VINAS.
|
|
14:15 - 14:50 |
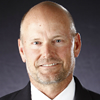 |
- Optimizing Mesh Topology for CFD Solution Efficiency and Accuracy
- Richard J Matus, Ph.D. Executive Vice-President, Pointwise, Inc.
- The importance of mesh topology in determining total CFD and optimization cycle time and accuracy of results will be discussed and then demonstrated through application to automotive, marine, wind energy, and aerospace example cases.
|
|
14:50 - 15:05 |
Coffee Break |
15:05 - 15:35 |
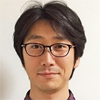 |
- High-Order unstructured meshing for Large-Eddy Simulation (LES)
- Mr. Takanori Haga, Doctor of Engineering
Research Engineer, Research and Development Directorate, Research Unit III, Japan Aerospace Exploration Agency
- In recent years, LES using high-order unstructured mesh methods is getting to be spread. These methods with a degree of freedom inside the cell can provide a high-resolution solution even on a coarse mesh. On the other hand, it was a challenge to generate the high-order mesh that faithfully represents the curved surface shape.
This presentation will introduce case studies using higher-order meshes created on Pointwise V18.2.
|
|
15:35 - 16:10 |
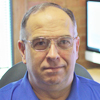 |
- Research into H- and P-Adaptation at Pointwise.
- Dr. Steve L. Karman Jr., Staff Specialist, Advanced Research, Pointwise, Inc.
- Pointwise is developing techniques for performing H-P Adaptation under a NASA Phase II contract. H-adaptation involves adding additional points to the mesh and increasing the number of elements. P-adaptation involves changing the order of elements by adding additional points to the elements and changing the order of the polynomial that represents the solution within the element. The combination provides increased resolution for use with Finite Element flow solvers.
|
|
16:10 - 16:45 |
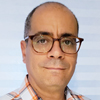 |
- Meshing & Adaptive Re-meshing Server for automated analysis & optimization using Pointwise
- AMINE Ben Haj Ali , Ph.D., M.Eng.
Senior Engineering Specialist, Advanced Aerodynamics, BOMBARDIER Inc.
- MARS (Meshing & Adaptive Re-meshing Server) is developed at Bombardier as a third generation (object-oriented) templated mesh generation toolkit using Pointwise®.
From conceptual perspective, MARS development is driven by industrial requirements such as modularity, quality, efficiency, repeatability, consistency, accuracy, and optimization enablement.
|
|
16:45 - 16:50 |
Coffee Break |
16:50 - 17:50 |
Keynote Speech |
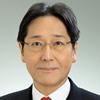 |
- Fluid Informatics 2.0
- Professor Shigeru Obayashi
Director, Institute of Fluid Science, Tohoku University
- The collaboration of engineering fields and Informatics is becoming the important function to develop Society 5.0. In this presentation, the latest development of "Fluid Informatics" will be introduced.
|
|
17:50 - 18:00 |
- Closing Speech
- Yasuhiko Fujikawa, President & CEO, VINAS Co., Ltd
|
18:00 - 19:30 |
Reception Party |
- A fantastic opportunity for sharing and exchanging information with each other.
- -Venue: Tokyo Conference Center Shinagawa – 5th floor foyer[in front of the grand hall]-
*Please notify your attendance at the time of registration. |
-Please note the program may change without prior notice.
-Company and product names are trademarks or registered trademarks.
Hall B:Design Optimization・High Speed Calculation・Workflow |
9:00 - 9:30 |
Registration |
9:30 - 9:55 |
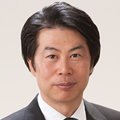 |
- (Broadcasting) Opening
- Yasuhiko Fujikawa, President & CEO, VINAS Co., Ltd
-
|
9:55 - 10:10 |
- High-Performance Computing and Cloud Computing supporting service
- Kenji Morimoto, Project Development Department, VINAS Co., Ltd.
- Introduce our efficient solutions for High-Performance Computing and Cloud Computer, such as the development of HPC applications, parallelization and acceleration tuning, the building of automation systems, and tools for conveniently using HPC and networks.
|
|
10:10 - 10:40 |
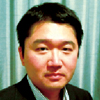 |
- A hybrid approach for elucidating multi-conformational states of biomolecules by combining experimental data and simulation
- Mr. Atsushi Tokuhisa, Ph.D.
Research Scientist, RIKEN Cluster for Science, Technology and Innovation Hub(RCSTI), RIKEN
- We are developing a method for estimating plausible three-dimensional structural model of biomolecules by combining single-particle experimental data and simulation aiming to apply it to drug discovery. In this presentation, we will introduce our hybrid approach called the diffraction template-matching method for elucidating multi-conformational states of biomolecules from noisy incomplete data set.
|
|
10:40 - 10:50 |
Coffee Break |
10:50 - 11:05 |
- Shape Design Optimization using mesh/geometry morphing and highlight of upcoming version Sculptor V3.9
- Yukihiro Yamamoto, Engineering Department 2, VINAS Co., Ltd.
- Functionality of Sculptor, design optimization package system for designers, and its case study will be shortly shown in this presentation. And the highlight of the new functions of the next version Sculptor V3.9 in the run up to presentation by Mark Landon, Ph.D., Optimal Solutions Software.
|
|
11:05 - 11:40 |
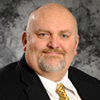 |
- Sculptor V3.9
New Features and Capabilities in Sculptor.
Recent Examples From Motorsports, Diesel Engines,
and Turbine Blade Design and Repair.
- Mark D. Landon, Ph.D. Chief Technical Officer, Optimal Solutions Software, LLC
- Sculptor V3.9 will be unveiled. Examples of exciting shape optimization and shape matching results will be shown from Sculptor users at Pratt&Whitney, Cummins, and HarleyDavidson. New tools have been added to Sculptor for better Arbitrary Shape Deformation (ASD) creation and defining Shape Change variables. Even though our ASD provides very smooth volumetric morphing, mesh healing and smoothing functions are now available. Sculptor’s Shape Matching feature is applied to an actual turbine blade manufacturing processes to ensure each blade’s actual manufactured shape is analyzed for CFD and/or FEA performance criteria. The shape design of turbine blade blends helps extend the life of jet engines.
|
Pratt&Whitney In-house developed solver
|
11:40 - 12:10 |
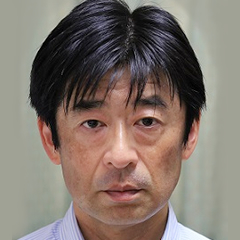 |
- Optimization examples of air-conditioning fan shape designs using SCULPTOR
- Mr. Tsuyoshi Eguchi
Team Manager, Air-Conditioner Designing & Engineering Department, Mitsubishi Heavy Industries Thermal Systems, Ltd.
- Presented are examples of optimizing the shape of a propeller fan using SCULPTOR.
We investigated the optimized blade shape based on a parametric study conducted by the experimental design method using the fan input under the same air flow conditions as the objective function.
|
|
12:10 - 13:20 |
Lunch & Demo |
13:20 - 13:40 |
- Integrated total optimization design solution service provided by VINAS
- Nobuyuki Suzuki, Engineering Department 2, VINAS Co., Ltd.
- Introducing iDIOS providing for multi-objective optimzation and exploration algorithms which developed by domestic research institutes based on over 20 years of optimal design experience by VINAS. In addition, we will introduce optimal design solutions based on iDIOS across multiple design areas such as parametric shape optimization by mesh morphing using Sculptor and topology shape optimization by Helyx-Adjoint.
|
iDIOS -CHEETAH -iSPM -DAKOTA -WHEEL -Vharmo
|
13:40 - 14:10 |
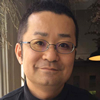 |
- Status update of the multiobjective design optimization engine CHEETAH/R
- Associate Professor Akira Oyama
Institute of Space and Astronautical Science, Japan Aerospace Exploration Agency
- We are developing the next-generation multiobjective design optimization engine CHEETAH/R in the Post-K project. CHEETAH/R is based on CHEETAH developed by the HPCI strategic program and incorporates new technologies such as domain decomposition to obtain better solutions for design optimization problems with severe constraints.
|
|
14:10 - 14:40 |
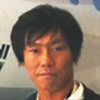 |
- Optimization method using surrogate models and implementation in JAXA's Harmonee-sa
- Associate Professor Masahiro Kanazaki, Ph. D. (Information Science)
Graduate School of System Design, Metropolitan University / Guest Researchers, Japan Aerospace Exploration Agency
- This section outlines and introduces a high-efficiency optimization method based on the surrogate models method implemented in the optimization algorithm provided as JAXA Harmonee-sa. Since the approximation of the objective function does not require the gradient of the objective function, it is less dependent on problems and evaluation methods and can be used for experiments as well as simulations. We will talk about strengths such as low evaluation man-hours, high efficiency and usability.
|
|
14:40 - 14:50 |
Coffee Break |
14:50 - 15:30 |
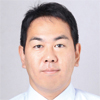 |
- Method of Multi-Objective Design Optimization on automotive aerodynamics and underhood cooling air flow
- Mr. Atsushi Itoh
Vehicle Function Testing Dept., Mitsubishi Motors Corporation
- Using Design Exploration Software, iDIOS-CHEETAH, large scaled multi-objective optimization system has been developed, and its system is applied to get pareto solutions on automotive aerodynamics and underhood cooling air flow. A presentation on them will be given in the session.
|
|
15:30 - 15:45 |
- Building morphing model for real complex shape of automotive vehicle with Sculptor
- Ms. Emi Matsumoto
Vehicle Function Testing Dept., Mitsubishi Motors Corporation
Yukihiro Yamamoto, Engineering Department 2, VINAS Co., Ltd.
- To conduct multi-objective design optimization with large-scaled CFD analysis on automotive performances, high precision mesh morphing model is built by Sculptor so complicate deformation of automotive vehicle can be available. In this session, some examples will be introduced.
|
|
15:45 - 16:15 |
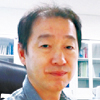 |
- Tool development to support "Analyzing a phenomena"
- Professor Kenji Ono
Director, Research Institute for Information Technology, Kyushu University
- Simulation and data science have different approaches toward deduction and induction to science, but this complementary use of both approaches will open up a new paradigm by synergies. Some examples of this approach for modeling that is important to understand the phenomenon will be introduced.
|
|
16:15 - 16:45 |
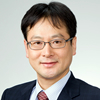 |
- Automotive aerodynamics CAE by integration of HPC Simulation and Data Science
- Professor Makoto Tsubokura
Center for Computational Science, RIKEN / Graduate School of System Informatics, Kobe University
- By use of massive data obtained from high-end super computer, a new CAE can be created. In this session, the case of multi-objective shape optimization for automotive aerodynamics on the K computer will be shown, and then post processing method using modal analysis based on the CFD results will also be shown, and application of machine learning toward producing a research outcome on the super computer "FUGAKU" will be discussed.
|
|
16:45 - 16:50 |
Coffee Break |
16:50 - 17:50 |
(Broadcasting) Keynote Speech |
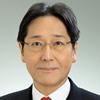 |
- Fluid Informatics 2.0
- Professor Shigeru Obayashi
Director, Institute of Fluid Science, Tohoku University
- The collaboration of engineering fields and Informatics is becoming the important function to develop Society 5.0. In this presentation, the latest development of "Fluid Informatics" will be introduced.
|
|
17:50 - 18:00 |
- Closing Speech
- Yasuhiko Fujikawa, President & CEO, VINAS Co., Ltd
|
18:00 - 19:30 |
Reception Party |
- A fantastic opportunity for sharing and exchanging information with each other.
- -Venue: Tokyo Conference Center Shinagawa – 5th floor foyer[in front of the grand hall]-
*Please notify your attendance at the time of registration. |
-Please note the program may change without prior notice.
-Company and product names are trademarks or registered trademarks.