 |
9:30 - 9:55 |
- CRUNCH CFD V1.0 - A highly accurate CFD solver with advanced features
- Takeru Fukuchi, Ph.D., General Manager, Engineering Department 2, VINAS Co., Ltd.
- This session presents CRUNCH CFD V1.0 solver and its application examples. Based on advanced technologies developed for NASA, this solver specializes in fluid physics that other general purpose solvers can not be applied to.
|
 |
9:55 - 10:35 |
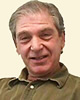 |
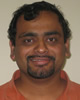 |
- Multi-disciplinary Applications of CRUNCH CFD for Aeroacoustics and Flow Control
- Dr. Sanford.M.Dash, President & Chief Scientist
Dr. Srinivasan Arunajatesan, Senior Research Scientist
Combustion Research and Flow Technology, Inc. (CRAFT Tech)
|
 |
In this presentation, recent modeling activities at CRAFT Tech of aeroacoustic flowfields will be presented. The focus will be on modeling of near field surface dynamic loads and control of these dynamic loads. Open loop control and closed loop adaptive control including detailed actuator modeling and integration of controller and system identification algorithms within the CFD framework will be discussed |
10:35 - 11:15 |
 |
- Application of CRUNCH CFD for Combusting and Multi-Phase Cryogenic Fluid Systems
- Dr. Ashvin Hosangadi, Principal Scientist, Combustion Research and Flow Technology, Inc. (CRAFT Tech)
|
 |
Simulations of high-pressure, fluid systems operating close to the critical temperature will be presented. In this regime fluid thermodynamics exhibit strong non-ideal effects which can significantly affect the flow physics. Examples will range from cavitating cryogenic inducers and feed system components to supercritical combustors with gas-liquid jet interactions. |
11:15 - 11:50 |
- Introduction of a combustion analysis solver CONVERGE
- Shinichi Oka, Manager, Applied Research for Advanced Technology, VINAS Co., Ltd.
- This session presents CONVERGE, an engine combustion analysis solver featuring fully automatic mesh generation capability. The solver is developed by researchers from University of Wisconsin Engine Research Center who are known for distinguished research in spray and combustion in engines.
|
 |
11:50 - 13:10 |
Lunch / Demonstration *Short presentation |
 |
13:10 - 13:30 |
- Enhance your CFD-based design optimization process by SCULPTOR V2's "Back2CAD" function
- Yukihiro Yamamoto, Technical Marketing Group, Engineering Department 1, VINAS Co., Ltd.
- New features of SCULPTOR V2 are presented in this session, including Back2CAD function which enables output of optimized design shape after geometry morphing back to CAD, as well as functions that are used for achieving higher efficiency in definition of morphing setting.
|
 |
13:30 - 14:10 |
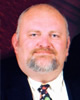 |
- SCULPTOR's New Features, Capabilities, Applications, and Success Stories from Around the World
- Mr. Mark D. Landon, Ph.D., Chief Technical Officer, Optimal Solutions Software
|
  |
A presentation and demonstration of SCULPTOR's Version2.2 with its new Back2CAD, free-form deformation of CAD models, Cylindrical Arbitrary Shape Deformation (CASD), Shape Matching, Fluid&Thermal Structure Interaction, and much more. CASD is a new breakthrough to deform cylindrical models such as turbo machinery. Back2CAD can apply the same deformation as achieved with CFD/FEA shape optimization back to the CAD model. Real-time deformation of CAD models with the same ease, efficiency, and accuracy as Sculptor has heretofore applied to CFD/FEA mesh models. Many new translators to CFD/FEA/CAD formats have been developed. Exciting example with SCULPTOR and ConvergeCFD will be displayed. |
14:10 - 14:50 |
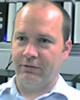 |
- Optimisation of a Road Car Using RANS and DES CFD Models
- Dr. Rob Lewis, Managing Director, TotalSim Limited
|
 |
Traditionally the motor industry has used the Reynolds Average Navier-Stokes (RANS) CFD model to quickly create a steady state approximation of the air flow past road vehicles. As it is possible to run a large number of RANS models in a short period of time, more companies are using RANS CFD models to optimise their designs.
Whilst RANS codes can produce accurate results for attached flows, the same cannot necessarily be said if the flow is heavily separated. In order to produce a more accurate CFD solution for separated flows, a more computationally costly Detached Eddy Simulation (DES) can be used. Ever increasing computer power has meant that DES has become a viable tool for analysing car aerodynamics however the computer run time has meant that DES is not used in the motor industry for full car optimisation.
This paper details a study where the geometry of a small family car was optimised to minimise drag. This study was undertaken using both RANS and DES so that comparisons can be made between the two modeling techniques looking at the different flow structures predicted, and ultimately the differences in the optimised geometries predicted by the two methods.
|
14:50 - 15:20 |
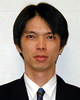 |
- Design optimization examples of turbomachinery equipment
- Dr. Shigeyuki Tomimatsu, Research and Development Center, DMW Corporation
|
 |
DMW Corporation conducts many analyses on fluid equipment including pumps, blowers and related equipment by using Gridgen, FieldView and SCULPTOR. This session presents examples of design optimization using SCULPTOR. |
15:20 - 15:40 |
Coffee Break & Demonstration |
 |
15:40 - 16:10 |
- Supporting designers and experts in turbomachinery performance evaluation and in improvement of design work efficiency by thermo-fluid analysis system FINE/Turbo V8
- Yoshiyuki Sawa, General Manager, Engineering Department 1, VINAS Co., Ltd.
- Turbomachinery CFD system FINE/Turbo improves design performance by advanced analysis technology and enhances efficiency by automatic mesh generation tools. This session presents its new functions, as well as information about future development roadmap of FINE series and VINAS's turbomachinery CFD engineering service.
|
 |
16:10 - 16:30 |
- Highly efficient turbomachinery design by 3D inverse solver system TURBOdesign Suite 3.1
- Yukihiro Yamamoto, Technical Marketing Group, Engineering Department 1, VINAS Co., Ltd.
- TURBOdesign Suite 3.1 enables high performance turbomachinery design that surpasses former experience-based designs by its easily managed 3D inverse solver. This session presents its application example in which performance of turbomachinery was improved by adjusting load setting of blades and therefore the flow field.
|
 |
16:30 - 16:40 |
Break |
16:40 - 17:20 |
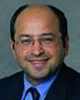 |
- Methodologies for rapid 3D multi-objective/multi-point optimization of turbomachinery blades
- Prof. Mehrdad Zangeneh, Director, Advanced Design Technology ltd
|
 |
Two methodologies are presented for 3D multi-objective optimization based on using a 3D inverse design method. The application of the methods to various multi-objective design problems in pumps, compressors and fans are presented. |
17:20 - 17:50 |
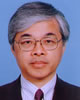 |
 |
- Multi-objective design optimization of turbomachinery by TURBOdesign-1 and CFD
- Dr. Akira Goto, Deputy Division Executive/Mr. Watanabe Hiroyoshi, Fluids Engineering Group Manager
Fluid Machinery Development Division, Technology Development Department, Fluid Machinery & Systems Company, EBARA Corporation
|
 |
This session first presents an example of product developments by 3D inverse design code TURBOdesign-1 and CFD, and then an example of multi-objective design optimization of high specific-speed mixed flow pump where meridional geometry and blade loading are design parameters and maximum efficiency, stall characteristics and shut-down performance are objective functions. |
17:50 - 18:00 |
- Closing Speech
- Yasuhiko Fujikawa, President & CEO, VINAS Co., Ltd.
|
-Please note the program may change without prior notice.
-Company and product names are trademarks or registered trademarks.