 |
10:00 - 10:30 |
- Opening Speech
- Yasuhiko Fujikawa,
President & CEO, VINAS Co., LTD
|
10:30 - 10:45 |
- Enabling parallel visualization in average engineering environment - FieldView 12.3 and its future development plans
- Masaya Tani,
Pre-Post Consulting Group, Engineering Department 1, VINAS Co., Ltd.
- Overview of the latest version of FieldView, which enables efficient visualization of large-scale CFD analysis in engineering departments by utilizing computing hardware with multi-core CPUs. In addition, user examples in Japan and from overseas will be presented.
|
 |
10:45 - 11:15 |
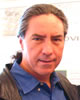 |
- Creating Effective CFD Workflows via Automated and Extract-Based Postprocessing
- Mr. Matthew N. Godo, Ph.D.
,FieldView Product Manager, Intelligent Light
|
 |
Today, CFD users are forced to face the challenge of effectively postprocessing their data in a timely and productive manner within compute environments which are becoming increasingly powerful. Extract-based workflows, continuously being developed at Intelligent Light, will be presented outlining the latest advances in co-processing and upstream CFD planning. |
11:15 - 11:55 |
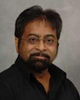 |
- Large-Eddy Simulation for Predicting Low-Emission Combustion and Lean Blowout in Gas Turbine Engines
- Dr. Suresh Menon
Professor, School of Aerospace Engineering, Georgia Institute of Technology
|
 |
Simulation of turbulent combustion in practical devices is very complex due to the wide range of scales involved: from the molecular scales where mixing and combustion occurs to the large-scale of the device that control the global processes. For next generation low-emission gas turbine engine (used for both propulsion and power generation), a design goal is to operate in the very lean limit but this has problems related to fuel-air mixing, lean blowout (LBO) and combustion instability. To optimize design, simulation must study operating conditions from stable to unstable combustion, without any ad hoc adjustment to the model. In this talk, a multi-scale approach will be discussed that can handle these requirements within a single modeling framework. Successes (and failures) as well as areas for future investigations will be identified. |
11:55 - 12:05 |
Break |
12:05 - 12:35 |
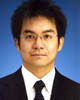 |
- Remote parallel visualization of unsteady CFD results for R&D of spacecraft
- Dr. Seiji Tsutsumi
Engineer, JAXA's Engineering Digital Innovation (JEDI) Center, JAXA
|
 |
Unsteady CFD analyses are conducted for R&D of spacecraft by using JAXA Supercomputer System (JSS) located in Chofu Aerospace Center. In this presentation, remote and parallel visualization methodology using PC cluster and advanced software, such as FieldView, is introduced. This method allows us to analyze the unsteady results obtained by the JSS from remote site (Sagamihara Campus). |
12:35 - 13:05 |
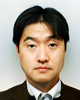 |
- Visualization of large-scale unsteady CFD analysis results using FieldView Parallel
- Mr. Masaya Tsunoda
Manager, Research and Development, HQ Research Dept. 1, Sumitomo Rubber Industries, LTD.
|
|
In Sumitomo Rubber, we develop our own proprietary CFD solver, and one of the most difficult challenges is how to handle analysis results with a computational grid of several hundred million points or more. Fortunately, FieldView Parallel has all necessary features to solve this problem. In this presentation, advantages of FieldView Parallel are discussed from a user’s viewpoint. |
13:05 - 14:35 |
Lunch / Demonstration |
14:35 - 14:55 |
- Co-sponsored Speech
Supporting high-performance computing by enhanced efficiency - IBM System x iDataPlex
- Mr. Hideyuki Kamemoto
System x, IBM Japan, Ltd.
- IBM System x iDataPlex enjoys a favorable reputation in the marketplace for its high performance and enhanced efficiency. Summary of the product and related services will be presented.
|
|
14:55 – 15:15 |
- Verification and application of CFD analysis of spray and combustion in an engine cylinder by CONVERGE V1.3
- Takeru Fukuchi, Ph.D.
Engineering Department 2, VINAS Co., Ltd.
- CONVERGE V1.3 is an innovative CFD tool for analysis of spray and combustion in engine cylinders, which enables reduction of user time and increase of analysis accuracy at the same time. This presentation provides verification of the software tool and its application examples.
|
 |
15:15 – 15:45 |
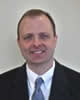 |
- Recent developments of CONVERGE CFD software for rapid and accurate in-cylinder spray and combustion modeling
- Mr. Eric Pomraning, Ph.D.
Vice President, Convergent Science Inc.
|
|
CONVERGE CFD software is used to simulate the flow, spray and combustion found within various internal combustion engines. Recent CONVERGE developments in terms of both physical modeling and solution speedup will be presented. Elimination of mesh generation will be outlined. |
15:45 – 16:05 |
Coffee Break / Demonstration |
16:05 – 16:20 |
- Engine ICD Reporter – An automatic reporting system of engine CFD analysis results
- Hiroyuki Suzuki
Pre-Post Consulting Group, Engineering Department 1, VINAS Co., Ltd.
- An overview and demonstration of “Engine ICD Reporter” (an add-on program for FieldView), which automatically performs visualization tasks of combustion analysis results of engine cylinder.
|
 |
16:20 – 17:00 |
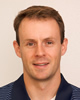 |
- Simulation of Two-Stroke Opposed Piston Diesel Engine
- Mr. Tristan M. Burton, Ph.D.
Senior Staff Scientist, Achates Power
|
 |
CONVERGE is applied to the full-cycle simulation of a two-stroke opposed piston diesel engine. The simulation results are used to provide detailed information about in-cylinder flow motions, scavenging, and manifold pressure dynamics. |
17:00 – 17:30 |
- Overview and examples of CAD data acquisition and open-source optimization system using SCULPTOR V2.3
- Yukihiro Yamamoto
Technical Marketing Group, Engineering Department 1, VINAS Co., Ltd.
- This presentation covers an example of acquiring CAD data of optimized design by using mesh morphing capability of SCULPTOR, and an example of multi-objective shape optimization conducted by a collaboration of an open-source optimization system and SCULPTOR.
|
 |
Keynote Speech |
17:30 – 18:10 |
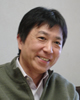 |
- Collaboration of CFD and HPC - a Clue for Innovative Conceptual Design
- Professor Kozo Fujii
Deputy Director General, Institute of Space and Astronautical Science, JAXA
|
|
I flashed back the history of CFD in the opportunity I was given at the VINAS UGM three years ago. In my presentation this time, what happened in the following three years will be summarized and CFD in industries 10 years from now will be discussed. In the Next-generation supercomputer project in Japan, five application areas were strategically selected. Area No. 4 is "technology use" and our group will start two application projects in this strategy plan. By introducing these two projects, future use of CFD in industries will be discussed in the presentation. |
Reception Party |
18:10 – 20:00 |
- Please join! This is a good opportunity for sharing and exchanging information with each other.
- - Venue: Tokyo Conference Center Shinagawa - 5th floor foyer [in front of the grand hall] -
*Please notify your attendance at the time of registration. |
-Please note the program may change without prior notice.
-Company and product names are trademarks or registered trademarks.
 |
10:00 - 10:30 |
- Opening Speech (Broadcasting)
- Yasuhiko Fujikawa,
President & CEO, VINAS Co., LTD
|
10:30 – 10:40 |
- VINAS’s approach toward efficiency improvement of weight reduction and design optimization process
- Toru Sugino
Director, Head of Tokyo Office, VINAS Co., Ltd.
|
|
10:40 – 10:55 |
- Overview of TOSCA 7.0.2 – Supporting acceleration of weight reduction design process
- Hidetoshi Takaoka
Engineering Department 3, VINAS Co., Ltd
- Working together with a general purpose structural analysis solver, TOSCA accelerates design process by calculating light-weight geometry which satisfies multiple design objects in only one cycle of optimization process. In this presentation, features of TOSCA will be overviewed.
|
 |
10:55 – 11:30 |
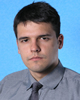 |
- Weight Reduction with TOSCA.Structure in the Existing CAE Environment. Functions and Improvements of the Latest Version
- Mr. Chavdar Georgiev
Dipl. -Ing., FE-DESIGN GmbH
|
 |
The increasing global competition requires that leading companies use the best technology to keep their market position. Demands on production and development are stronger than ever. FE-DESIGN is technology leader in topology/shape/bead optimization since many years and helps customers worldwide to improve their products in the complete product development process. Using TOSCA Structure it is possible to optimize in the existing CAE environment huge structures (e.g. millions of elements), to consider non-linearities (large deformations, contact, non-linear materials) or to integrate fatigue results in order to minimize damages. Various manufacturing constraints are available, to get producible design proposals. Industrial case studies will show different approaches to achieve results in a fast and efficient manner. |
11:30 – 12:05 |
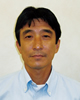 |
- Application examples of TOSCA for design of structural members of construction machinery
- Mr. Kazuhisa Tamura, General Manager
Experiment, Analysis & Evaluation Center, Development & Production Group
Hitachi Construction Machinery Co.,Ltd
|
|
Traditionally, optimization (achieving both functional improvement and cost reduction at the same time) of main structure members of construction machinery (plate workings, castings, forged parts, etc.) has been based on past experiences, knowledge, experiments, and simulations. Now, as a new way of optimization, Hitachi Construction Machinery is applying non-parametric topology optimization in which non-linear characteristics, buckling behavior, and quality of material are considered. Application examples and benefits of this method, as well as its possibility in application in actual design will be presented. |
12:05 – 12:40 |
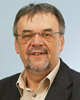 |
- Alternative Energy Generation to reduce CO2 Emission by optimizing Wind Turbine Components with “TOSCA.Structure”
- Mr. Manfred Fritsch
Dipl. -Ing., FE-DESIGN GmbH.
|
 |
Generally, the present lecture addresses the challenging topic of obtaining new conceptual designs for structural wind turbine components and/or improving the existing structural designs of wind turbines. For solving the above problems we recommend to use the structural automated optimization software TOSCA.Structure supplied by FE-DESIGN. |
12:40 – 13:50 |
Lunch / Demonstration |
13:50 – 14:25 |
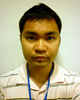 |
- Application examples of structural design optimization methods using TOSCA
- Mr. Akira Kobayashi
Mechanics Technology G. Mechanical Technology Dept. Products Development Center, IHI Corporation
|
|
IHI introduced TOSCA to take advantage of benefits in design optimization technology in the early stages of design/development processes. An example in which optimization result of a large structural part was reflected in the actual design will be presented, as well as another example in which optimized geometry of a ship part was obtained to achieve the best strength under multiple load cases. |
14:25 – 15:15 |
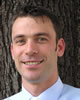 |
- Topology Optimization for Lightweight Crankcase Design of Medium-Speed Diesel Engines
- Mr. Peter Böhm,
Deputy Senior Manager - Engineering Mechanics – Vibrations, MAN Diesel & Turbo SE
|
 |
MAN Diesel & Turbo SE has successfully integrated the topology optimization technology into the design process of a crankcase of medium-speed diesel engines. The new crankcase design reveals significant weight reduction while ensuring a number of requirements with respect to stiffness and dynamics. This has become feasible as topology optimization has matured to a tool handling large problem size, large number of load cases and a large number of manufacturing and symmetry conditions simultaneously. |
15:15 – 15:30 |
Coffee Break / Demonstration |
15:30 - 16:05 |
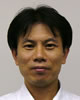 |
- Shape optimization of suspension parts with TOSCA
- Mr. Hideki Sugiura
Senior Researcher, Vehicle Mechanism Lab., Vehicle & Biomechanics Systems Div.
Toyota Central R&D Labs., Inc.
|
|
Torsion beams are main parts of automotive suspensions, and the latest trend is manufacturing them by using pressed pipes. Difficulties in designing this part due to its complex shape was overcome when we used TOSCA to come up with the optimized design to achieve necessary torsional stiffness while reducing the stress at the same time. |
16:05 – 16:40 |
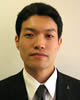 |
- Structural optimization of products exposed to dynamic load with a consideration on fatigue life
- Mr. Kazumasa Kato
Sales & Engineering, Magna Powertrain, Magna International Japan Inc.
|
 |
Fatigue life optimization was performed for a product which is exposed to dynamic load by using fatigue life prediction software FEMFAT and a mechanism analysis software in a structural design optimization process of TOSCA. |
16:40 – 17:30 |
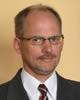 |
- New methods for the multi-disciplinary shape optimization of a rear wheel carrier
- Mr. Matthias Metschkoll
Mechanical Design Engineer, Numerical Simulation, Total Vehicle Architecture and Integration
Bayerische Motorenwerke AG
|
 |
Aiming for an increase in performance a sustainable lightweight design is a key requirement. To achieve this aim a multi-disciplinary shape optimization of chassis components was carried out on the current BMW 7 Series. |
Keynote Speech (Broadcasting) |
17:30 – 18:10 |
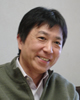 |
- Collaboration of CFD and HPC - a Clue for Innovative Conceptual Design
- Professor Kozo Fujii
Deputy Director General, Institute of Space and Astronautical Science, JAXA
|
|
I flashed back the history of CFD in the opportunity I was given at the VINAS UGM three years ago. In my presentation this time, what happened in the following three years will be summarized and CFD in industries 10 years from now will be discussed. In the Next-generation supercomputer project in Japan, five application areas were strategically selected. Area No. 4 is "technology use" and our group will start two application projects in this strategy plan. By introducing these two projects, future use of CFD in industries will be discussed in the presentation. |
Reception Party |
18:10 – 20:00 |
- Collaboration of CFD and HPC - a Clue for Innovative Conceptual Design
- Professor Kozo Fujii
Deputy Director General, Institute of Space and Astronautical Science, JAXA
|
-Please note the program may change without prior notice.
-Company and product names are trademarks or registered trademarks.