DAY1/October 5th, 2022 / Wed 10:00 - 16:55 |
10:00 - 10:20 |
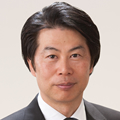 |
- Opening Remarks - New products and services this year for large-scale, high-speed, high-precision analysis and optimal design
- Yasuhiko Fujikawa, President & CEO, VINAS Co., Ltd
- This year again, we will present the latest information on each solution for large-scale, high-speed, and high-precision analysis, along with examples of use in Japan and overseas. This year, we will also present a new product, OASIS, an AI-based optimal design system, which is said to be the next-generation optimization technology. OASIS allows users to find the optimal design intuitively, quickly, and easily by AI without having to select optimization algorithms or use complicated parameters or scripts. The product is widely used in design departments. We are pleased to announce the latest version V2 of VFBasis, which automatically extracts the critical vortex vibration modes that affect product performance.
|
10:20 - 11:20 |
Keynote Speech |
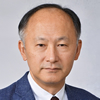 |
- Large Scale Coupling Simulations of Real Machines based on Partitioned Iterative Algorithms
- Professor Shinobu Yoshimura
School of Engineering, The University of Tokyo
- Various parallel dynamics analysis codes for fluid systems, structural systems, combustion systems, etc. are running in the state-of-the-art HPC environment such as Fugaku and are being used for solving large scale analysis of real machines. However, the coupled phenomena that are unavoidable in real machines are still only handled in small-scale and simple analysis on PCs and workstation environments. This presentation will introduce large-scale simulations of real machines based on partitioned iterative methods Professor Yoshimura and co-researchers have developed over more than 10 years, and it will introduce various application examples on Fugaku. Professor Yoshimura will also explain the knowledge and skills required for analysts when solving coupled problems of real machines based on his extensive experience.
|
|
11:20 - 11:30 |
Break |
11:30 - 11:45 |
- Introduction of "Hybrid Parallel" function implemented in FieldView and CAE post-process solution provided by VINAS.
- Hiroyuki Suzuki, Engineering Department 1, VINAS Co., Ltd.
- The "Hybrid Parallel Function" implemented in FieldView enables fast and efficient processing of large-scale CFD analysis results. In this session, we will introduce the capabilities of hybrid parallel, look back on the history of functional enhancements, and introduce various solutions, support, consulting, etc. that we provide.
|
|
11:45 - 12:15 |
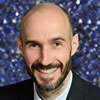 |
- FieldView 22 Update
- Mr. Yves-Marie Lefebvre, CTO, Tecplot, Inc.
- Our next release, FieldView 22, available this Fall, will introduce a number of improvements, including enhancements to FieldView’s unique Auto Partitioner, an all-new ANSYS-Fluent CFF reader, using HDF5, and a new transparent mode for streamlines and particles. Sections of the graphical user interface have also been streamlined to increase productivity.
|
|
12:15 - 13:15 |
Lunch & Demo |
13:15 - 13:45 |
- Effective Application of FieldView Parallel in CFD Workflows
- Mr. Yves-Marie Lefebvre, CTO, Tecplot, Inc.
- In this talk, we will use customer examples and workflow examples to illustrate where and how FieldView Parallel should be used in your CFD workflow for faster post-processing and loading ever larger data sets.
|
|
13:45 - 14:15 |
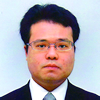 |
- Example of visualization using "FieldView" with "NuFD/FrontFlowRed
- Mr. Makoto Seino, Senior Researcher, CAE/CFD Development Group, Numerical Flow Design Inc.
- Numerical Flow Design, Inc. has been conducting analyses in various fields such as architecture, atmospheric environment, aerospace, machinery, nuclear power, etc. using the fluid analysis software "NuFD/FrontFlowRed".
We have used "FieldView" in many of these numerical analysis results. The graphical processing by "FieldView" is useful for understanding the phenomena, and we expect that the functionality will be enhanced to cope with the recent large-scale numerical analysis in the future. In this presentation, I will introduce the analysis cases we have conducted and the functions of "FieldView" used to clarify the phenomena. |
|
14:15 - 14:25 |
Break |
14:25 - 14:40 |
- The latest Version (1.6) and application of VFBasis
- Akio Kawaguchi,PH.,D. Engineering Department 3, VINAS Co., Ltd.
- VFBasis is the world's first commercial package system for fluid vibration/noise analysis by POD/DMD machine learning processing.
This is a tool developed to automatically extract and classify typical periodic fluctuation components that were difficult to analyze in large-scale and complex unsteady fluid analysis result data, and to facilitate analysis. As for features, it is possible to understand dominant fluid vibration phenomena and identify noise sources by extracting feature structures (spatial patterns) and their temporal changes (frequency, amplification factor) at high speed and with less memory. In this presentation, we will introduce the new functions of VFBasis V1.6 and application examples.
|
|
14:40 - 15:10 |
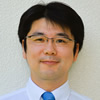 |
- Analysis of flow fields around automobiles using POD/DMD
- Associate Professor Takuji Nakashima
Graduate School of Advanced Science and Engineering, Hiroshima University
- In the current automotive aerodynamic analysis, huge amount of analytical results are now available due to the implementation of high-resolution and time-series analysis, and the importance of the techniques to extract essential information from such huge amount of data is increasing. In this presentation, two case studies are introduced. One is a fluctuating flow field analysis to investigate factors of aerodynamic force fluctuation acting on a vehicle body using mode decomposition technique with VFBasis. The other is a mode analysis to extract characteristic velocity distribution from aerodynamic analysis results of many vehicle shapes obtained in the optimization calculation process.
|
|
15:10 - 15:20 |
Break |
15:20 - 15:35 |
- Updates for Fidelity Pointwise 2022 and meshing service by Vinas
- Shunsuke Ohtsubo, Engineering Department 1, VINAS Co., Ltd.
- In recent years, Pointwise has enhanced the features that automatically provide the complex mesh control required for CFD simulations, while maintaining the bottom-up approach meshing. Not only does it generate meshes efficiently, but it also gives you consistent mesh control. In addition, the mesh can be modified flexibly using the way used to be. In this session, we will present the latest information on the new version Fidelity Pointwise 2022 and meshing services by VINAS.
|
|
15:35 - 16:05 |
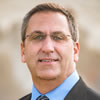 |
- Fidelity Pointwise Roadmap - Where we are, where we are going
-
Nick Wyman, Software Engineering Group Director, Cadence Design Systems, Inc.
Pat Baker, Software Engineering Director, Cadence Design Systems, Inc.
- Cadence continues to lead the industry in meshing for CFD by focusing on Automation, Acceleration, and Innovation in the meshing process. We will present new features delivered in recent product releases and those planned for future release. Examples will show how new meshing features are applied to industrial simulation.
|
|
16:05 - 16:55 |
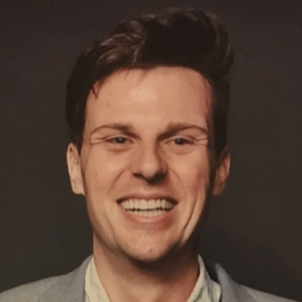 |
- Predicting High-Lift Aerodynamics on NASA Common Research Model - Part I: Reynolds Averaged Navier-Stokes Simulations
- NASA Ames Research Center, Jared Duensing
- An in-depth assessment of the High Lift Common Research Model (CRM-HL) aerodynamic performance is made using a Reynolds-Averaged Navier-Stokes (RANS) methodology within the Launch, Ascent, and Vehicle Aerodynamics (LAVA) framework. Results were produced in support of the 4th AIAA High Lift Prediction Workshop (HLPW-4), with additional simulation results and analysis used to support findings from the workshop. Mesh resolution, RANS closure models, and tunnel effects were among the sources of simulation sensitivity addressed, all in the pursuit of evaluating best-practice simulation methods for complex high-lift configurations. In general, free-air simulations using RANS yield accurate predictions of integrated loads in the pre-stall regime for the CRM-HL, while strong sensitivity to simulation method is observed near CLmax. Several available corrections for the Spalart-Allmaras (SA) turbulence model were tested and generally introduced more error relative to the experiment as compared to the baseline SA closure model. The Standard Menter Baseline Two-Equation (k-w BSL) turbulence model was also explored, which arguably yielded results highly consistent with experiment, but at a substantially higher computational cost. Therefore, as a compromise between computational cost and accuracy, the baseline SA closure model was selected for additional CRM-HL studies that assess alternative solution methods. These strategies include “warm start” approaches, unsteady calculations, and simulations that model the experimental wind tunnel. Results from these studies would reinforce the shortcomings of RANS in predicting aircraft performance at high-lift conditions, namely at high-a and highly loaded flap conditions, while also answering questions about appropriate modeling techniques to minimize the errors associated with RANS where possible.
|
|
Please note the program may change without prior notice.
-Company and product names are trademarks or registered trademarks.
DAY2/October 6th, 2022 / Thu 10:00 - 16:20 |
10:00 - 10:20 |
- CRUNCH CFD V3.4.1 and the application
- Akio Kawaguchi,PH.,D. Engineering Department 3, VINAS Co., Ltd.
- CRUNCH CFD is a high-precision fluid dynamics solver developed to analyze fluid phenomena that are out of the scope of conventional general-purpose solvers by packaging specialized technology accumulated in response to requests from NASA and the Department of Defense in the United States. Solver. High-precision analysis of phase change, combustion, cavitation of cryogenic hydrogen, fluid noise, and aerodynamics of car body/aircraft by applying the equation of state of real subcritical/supercritical fluids. Covers all velocities from supersonic to low-speed flow, and features robust solver technology that can stably obtain convergent solutions. A wide range of technical fields including aerospace, heavy industry, automobiles, various industrial machinery, and electronics and electronics that are working toward carbon neutrality. It can be used for design support and research and development.
|
|
10:20 - 10:50 |
 |
- Verification of Performance and Dynamic Behavior of 10 MWe Supercritical CO2 Compressor by Simulation and Actual Measurement
- Ashvin Hosangadi, Ph.D., Vice President, CRAFT Tech, USA
- This presentation will show Craft-tech's work in numerical analysis for the application of supercritical CO2 to power engines, which is expected to contribute to achieving carbon neutrality. Previous presentations have presented feasibility studies using CRUNCH CFD® for sub-scale models at Sandia Laboratories. In this presentation, we aim to make CRUNCH CFD® a highly accurate development support tool by verifying its accuracy with measured data on a 10 MWe compressor full-scale model and by improving its functionality. In addition, the effects of 2-phase flow behavior and inlet temperature on dynamic stability and compressor performance, which are important for design optimization, are also investigated.
|
|
10:50 - 11:00 |
Break |
11:00 - 11:30 |
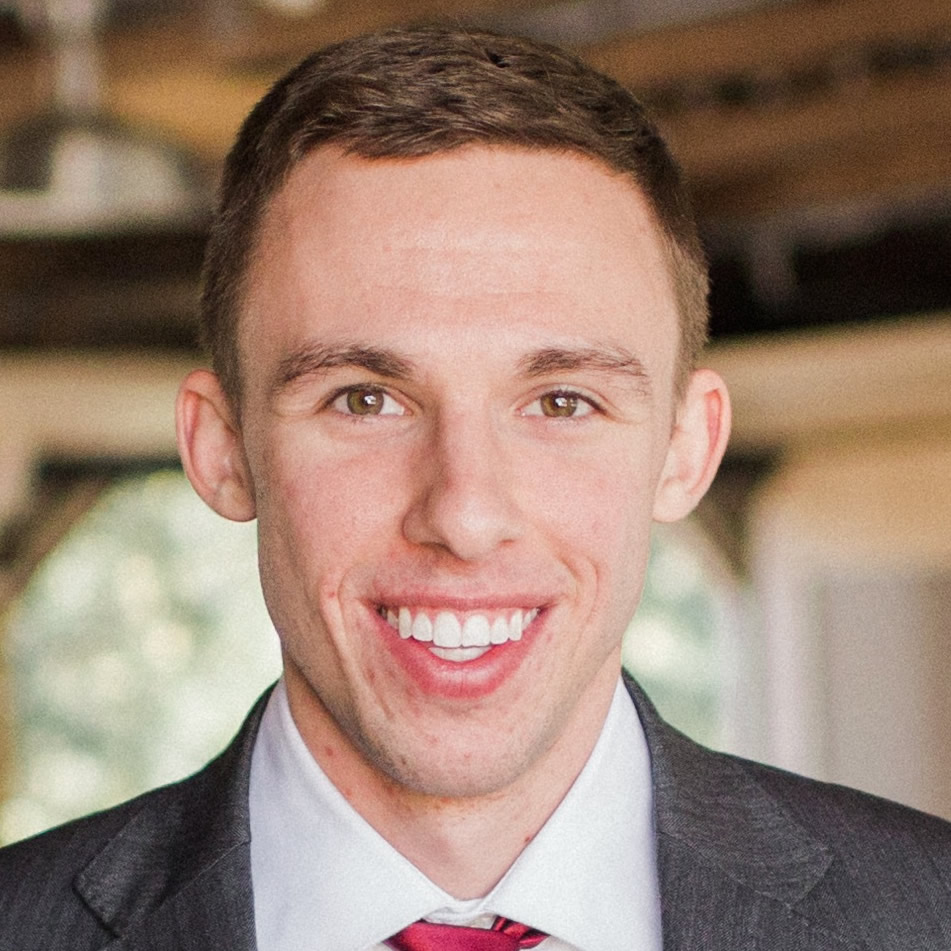 |
- Application of CRUNCH CFD to various optimization frameworks
- Tim Weathers, CRAFT Tech, USA
- In this presentation, we will introduce the application of optimization processes to improve the functionality and performance of various industrial products by utilizing the high-precision analysis capabilities of CRUNCH CFD® for complex physical phenomena. Examples will include cone shape optimization for decoking water jet nozzle performance improvement, hovercraft levitation fan efficiency improvement for driving force reduction, and wind turbine noise and efficiency trade-off optimization for wind power generation. It is shown that CRUNCH CFD® can be applied to the optimization process without sacrificing accuracy.
|
|
11:30 - 12:10 |
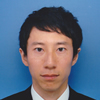 |
- Numerical Simulations of Supersonic Turbine for Rocket Engine Using CRUNCH CFD
- Keita Yamamoto, Ph.D
Researcher, Research and Development Directorate, Research Unit III, Japan Aerospace Exploration
Agency
- In recent years, various types of liquid rocket engines have been developed to achieve different types of mission. Turbine design is one of the most important factors since it determines an efficiency of rocket engine systems. In the present study, internal flow characteristics and performance of a rocket engine supersonic turbine are investigated by numerical simulations for several operating points with full admission and partial admission configurations.
|
|
12:10 - 13:10 |
Lunch & Demo |
13:10 - 13:30 |
- Overview of CFD on turbomachinery by HELYX and consulting services at VINAS
- Yoshiyuki Sawa, Engineering Department 1, VINAS Co., Ltd.
- HELYX is an integrated software package based on OpenFOAM , and developed to realize CFD analysis in the design field as an open source software. HELYX has been improved in many ways, including improved solver stability, enhanced mesh generation, and an easy-to-use GUI. In addition to the latest technological developments in HELYX and HELYX-Adjoint, VINAS provides support, training, and consulting services.
|
|
13:30 - 14:10 |
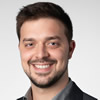 |
- HELYX 4.0: A New Chapter in Open-source CFD for Enterprise Applications
- Mr. Lisandro Maders, General Manager, ENGYS Brazil
- The expected launch of HELYX 4.0 in late 2022 will see the introduction of a new unified-solver framework to extend the current multi-region, multi-physics capabilities of the software. In this presentation we will preview the new features and CFD technologies developed by ENGYS® as part of this new version of HELYX in terms of meshing, solvers and visualization with a focus on real-life applications.
|
|
14:10 - 14:20 |
Break |
14:20 - 15:00 |
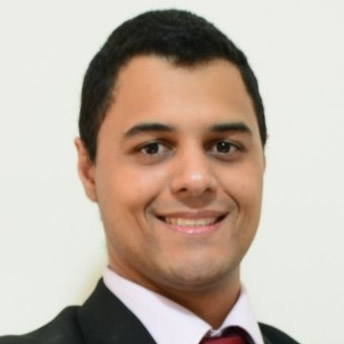 |
- CFD for HVAC Applications
- Mr. Gustavo Almeida, Senior CFD Enguinee, ENGYS Brazil
- The case studies of HVAC applications be introduced, including data center modelling, thermal comfort/stress at factory of outdoor power equipment and fire smoke analysis at train station.
|
|
15:00 - 15:40 |
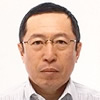 |
- Calculation of Internal Temperature Distribution during the Thermal Processing of Packaged Food
- Mr. Inaba Shoichi
Group Leader, Package & Heat Sterilization, Toyo Institute of Food Technology
- Packaged food such as canned foods must be inactivated heat-resistant bacterial spores in order to be preserved at ambient temperature for a long period. The food is heated at a temperature of around 120°C in filled and sealed state, so optimization of the heat heating and cooling temperature pattern is required to suppress deterioration of the foods. HELYX is used to conduct calculation of internal temperature distribution of packaged foods. This presentation will introduce the results showing good agreement between HELYX and experimental data.
|
|
15:40 - 15:50 |
Break |
15:50 - 16:20 |
- VINAS best solutions and consulting for high quality fluid analysis meshes tailored to the characteristics of CFD solvers, post-processing for efficient analysis of large CFD data and optimized design workflows with mesh morphing
- Emi Hatakeyama, Engineering Department
- VINAS has been providing solutions for CFD pre-post and optimization design since its establishment in 1996, with a focus on Pointwise, a high quality mesh generator for fluid analysis, FieldView, a CFD intelligent post processor, and Sculptor, a multi-purpose geometry parameter optimization design tool. We have been providing solutions for CFD pre-post and optimization design since our establishment in 1996. In particular, CRUNCH CFD, a CFD solver for clarifying fluid flow phenomena that cannot be handled by general-purpose solvers, and HELYX, an open source solver, are the best solutions for analyses that place high demands on mesh quality and post-processing of data that tends to be large in size. Pointwise and FieldView are recommended. Furthermore, for optimization design using SCULPTOR, etc., HELYX can be used to its advantage by running an unlimited number of analyses in parallel. In this session, we will reintroduce the pre-post optimization tools of VINAS solutions with CRUNCH CFD and HELYX as the main DAY2 and core CFD solvers, which strongly support the workflow around the workflow.
|
|
Please note the program may change without prior notice.
-Company and product names are trademarks or registered trademarks.
DAY3/October 7th, 2022 / Fri 10:00 - 17:30 |
10:00 - 11:00 |
Opening Special Lecture |
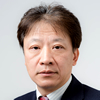 |
- HPC Industrial Use and Future Prospects in the Fugaku Era
- Professor Chisachi Kato
Institute of Industrial Science, The University of Tokyo
- A year and a half has passed since the common use of "Fugaku" started in March of the year before last. During this time, several achievements using "Fugaku" have been reported in the industrial world as well. In this presentation, the presenter will introduce the latest results of the "Program for Accelerating Achievements" which is a national project implemented by the presenter as a representative, and will look at the future industrial use of HPC.
|
|
11:00 - 11:10 |
Break |
11:10 - 11:30 |
- Introduction of solution services for efficient use of HPC
- Kazuhiro Hashiba, Project Development Department, VINAS Co., Ltd.
- Our HPC application services are promoted with a focus on calculation acceleration, system development, and cloud computer usage support. For computation acceleration, we provide consulting services such as numerical calculation program development and acceleration tuning. In system development, we provide automation and system construction services to streamline customers' workflows, such as pre- and post-processing and optimization workflows. In cloud computing application support, we provide tools and services for convenient use of computing resources such as in-house HPC, supercomputers, and cloud computing.
In this session, we will introduce solutions to efficiently utilize your HPC environment with a focus on the new CCNV6.0. |
HPC application developmen
|
11:30 - 12:00 |
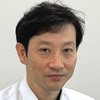 |
- Utilization of CCNV in a Hybrid HPC Environment
- Mr. Kyoji Ishikawa
Lead Engineer, ChAS Project Department Global Environment & Green Energy Project Operation Division, Chiyoda Corporation
- We build and operate an HPC environment as a hybrid of on-premises (including data centers) and the cloud at Chiyoda Corporation. Preparing and operating an environment that allows users of the HPC environment to select various methods using TUI and GUI according to their (user's) preferences and proficiency levels leads to smooth use of the HPC environment. This presentation will introduce examples of utilizing CCNV for job submission/management, data movement, etc. when using HPC.
|
|
12:00 - 13:00 |
Lunch & Demo |
13:00 - 13:50 |
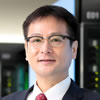 |
- Smart Design in the Society 5.0 Era Pioneered by Fugaku 2
- Professor Makoto Tsubokura
Center for Computational Science, RIKEN / Graduate School of System Informatics, Kobe University
- We introduce a new digital engineering technology that integrates CUBE, a unified simulation framework for complex phenomena being developed at RIKEN, and data science such as multi-objective optimization and machine learning. In this talk, I will introduce the current status of the development of the smart design system and the results obtained so far for four specific issues: automotive aerodynamic design, urban/architectural design, interior environment design, and combustion system design.
|
|
13:50 - 14:00 |
Break |
14:00 - 14:30 |
- The introduction of FOCUS Supercomputer New Q/R System and Fugaku New Usage System
- Dr. Takeshi Nishikawa
CTO/Supercomputing Professional/Chief Scientist,
CTO/Supercomputing Professional/Research Division, Foundation for Computational Science
- In this presentation, following item will be introduced:
- New Q (64 core)/R (32 core) system using AMD EPYC3 (Milan) CPU, which will be newly added to FOCUS Supercomputer from Autumn 2022
- “CCNV Center License" which is a GUI ssh client to be put into general use
- The new usage system of Supercomputer "Fugaku"
- Usage support (Industrial Use Project)
- First-touch option (Trial Project)
|
HPC application developmen
|
14:30 - 14:50 |
- Introduction to numerical software development service in VINAS
- Yoshinobu Akinaga, Project Development Department, VINAS Co., Ltd.
- VINAS provides contract services for the development of numerical calculation software in a wide range of fields from fluid and structural analysis to nuclear power and molecular science, the upgrading and functionalization of existing software, and the porting of applications to HPC environments such as the supercomputer "Fugaku" based on our high expertise and development technology cultivated in the HPC environment. We also provide contract services for porting applications to HPC environments such as the supercomputer "Fugaku". In this session, we will introduce recent development projects and examples of deployment of numerical applications to HPCI sites in Japan, including "Fugaku".
|
|
14:50 - 15:00 |
Break |
15:00 - 15:20 |
- An introduction of "OASIS AI", very rapid and familiar design optimization system utilizing AI/ML
- Yukihiro Yamamoto, Engineering Department 2, VINAS Co., Ltd.
- A new design optimization system which will be turned over, "OASIS AI," will be announced in the session.
"OASIS AI" is the design optimization system which is developed in the concept that there is no necessity to choose optimization algorithm and it takes less cost and effort to operate and setup the system, based on the assumption of designers use.
It can obtain relatively good solution of optimization in a remarkably short length of time, by utilize AI/ML in every aspect of its optimization process, for instance, selecting an optimization algorithm, derivation of relationship between design variables and objectives, and so on.
In this presentation, speaker will explain the outline of "OASIS AI", consisting of its simple functions and very familiar graphic interface.
|
|
15:20 - 16:00 |
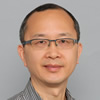 |
- Transforming Engineering with New AI
- Gary Wang, PhD, ASME Fellow, Distinguished Professor, Simon Fraser University, Vancouver, Canada
- Industries have seen great benefits of applying AI in their operations. Current AI technologies, however, have met challenges and limitations in practice. This talk will examine current AI technologies and point out directions for new AI technologies. The new AI is believed to transform engineering into the era of artificial world featured by advanced cyber-physical-social systems (CPSS). This talk will also give a practical example of applying small-data AI technologies for assembly plan optimization. AI-driven optimization is also compared against conventional optimization methods. In addition, a multi-national project on metal additive manufacturing will also be introduced.
|
|
16:00 - 16:10 |
Break |
16:10 - 16:30 |
- The latest status of the high-speed multi-objective design optimization system "iDIOS V2" and multi-objective shape optimization package "Sculptor 4.0"
- Yukihiro Yamamoto, Engineering Department 2, VINAS Co., Ltd.
- In this presentation, two products which are implemented "CHEETAH", the high-speed multi-objective design optimization algorithm developed in ISAS (Institute of Space and Astronautical Science), JAXA, will be shown.
"iDIOS V2" is the general-purpose optimization system which can conduct design optimization with various variables other than design variables on shape design. And it has implemented Application Program Interface to run in various workflow environment. By the new function, iDIOS-CHEETAH can be running in other commercial optimization software.
"Sculptor 4.0" is the software package for shape design optimization, and implements the gradient method as a single-objective optimization algorithm and Optimal Ratin Hypercube as DoE system other than CHEETAH.
Finally, the latest information on detail of the latest function in these products and VINAS's engineering service on design optimization.
|
|
16:30 - 17:20 |
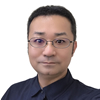 |
- The latest trend on multi-objective design optimization using machine learning
- Associate Professor Akira Oyama
Institute of Space and Astronautical Science, Japan Aerospace Exploration Agency
- In recent years, in proportion as machine learning as represented by deep learning has been attractings attention, there has been an increase in research on multi-objective design optimization using machine learning. Iin this presentation, the latest trend on multi-objective design optimization using machine learning will be introduced. In addition, aAs one example, a method for speeding up of computational fluid dynamic simulation using machine learning and an example of its application to aerodynamic design optimization will be reported.
|
|
17:20 - 17:30 |
- Closing Speech
- Yasuhiko Fujikawa, President & CEO, VINAS Co., Ltd
|
|
Please note the program may change without prior notice.
-Company and product names are trademarks or registered trademarks.